Три вида схеми за топене и наливане на ковко желязо
Пясъкът от смола от фуран обикновено се използва като формовъчен материал за мащабни отливки от ковък чугун, произведени в Китай. Произвежда се в едно цяло, с голямо тегло на изливане и сложна структура. Той има високи изисквания към качеството и производителността на отливките. Някои дефекти при леене, особено дефекти на свиване, често се появяват в процеса на топене. Това ще доведе до бракуване на отливката и ще причини големи икономически загуби, особено материала QT400-18AR, който има високи изисквания за якост, голямо удължение и стойност на удара.
Докато се гарантират механичните свойства на такива дебели и големи части, не е лесно да се избегнат графитни плаващи и свиващи се дефекти. Чрез проектирането на експерименти с проби, аналитичното оборудване на Elkem беше използвано за изследване на ефектите от химичния състав и температурата на изливане върху графита, плаващ, свиване и други дефекти на твърдата проба с дебелина на стената 180 мм. След това се прилага за производството на дебелостенни детайли от ковък чугун за получаване на отливки с добро качество.
Оборудването и материалите са подготвени за самостоятелно използване на чугун с висока чистота, чист нискоманганов скрап, високомагнезиев сфероидизиращ агент, 75#FeSi инокулант; Скероидизиращ агент с ниско съдържание на магнезий Elkem, инокулант; 1.5 тона пещ за топене с междинна честота, 500 кг сфероидизираща торба, 500 кг смесител. Термоанализатор Elkem EPIC, анализатор на въглерод и сяра, спектрометър. Размерът на дървения модел от твърда проба е 600 мм × 400 мм × 180 мм и процесът се произвежда пробно. Дебелината на стената от 180 мм се използва за покриване на дебели и големи сфероидни графитни чугунени продукти, произведени от компанията. Доста представително е. Оборудван е със система за щранг и шприц и приема дънен излив с тегло на изливане 500 кг.
Планът за топене и изливане е проектиран да използва пещ с междинна честота на топене 1.5 тона, за да разтопи 1.5 тона разтопено желязо, 500 кг всеки път, като инокулира със сфероиди, и да излее 1 кутия с малки проби. Общо 3 кутии с тестови парчета бяха изляти в 1 пещ. Различните схеми за топене и изливане са проектирани, както следва:
Съотношение на таксата за първата схема:
85% чугун, 15% нискоманганов стоманен скрап; контрол на химичния състав: приемане на план за третиране със сфероидизираща инокулация: първо, 500 кг желязо се доставя в чашата, а 1.3-1.5% високомагнезиев сфероидизиращ агент, 0.3-0.4% инокулант и инокулант са вградени в сфероидизиращия плик 0.8% покриващ агент, обърнете торбичката за сфероидизация. След като процесът на сфероидизация приключи, вътрешната повърхност на торбата се излива в поточния инокулант и се разбива напълно, след което пробата се анализира и тества с EPIC инструмент. 1.2% сфероидизиращ агент Elkem, 0.8-1.0% покриващ агент и 0.4% стъклен камък са вградени в сфероидизиращата торба, а желязото директно се изхвърля в сфероидизиращата торбичка и едновременно се поставя 0.5% инокулант Elkem. След приключване на сфероидизацията, последващият инокулант на Elkem, поръсен върху повърхността, ще бъде взет и анализиран с помощта на EPIC инструмент.
1.2% сфероидизиращ агент Elkem, 0.8-1.0% покриващ агент и 0.4% стъклен камък са вградени в сфероидизиращата торба, а желязото директно се изхвърля в сфероидизиращата торбичка и едновременно се поставя 0.5% инокулант Elkem. След завършване на сфероидизацията, последващият инокулант на Elkem, поръсен върху повърхността, ще бъде взет и анализиран с помощта на EPIC инструмент.
Съотношението на зареждане на втората схема: 65% чугун, 35% нисък манганов скрап; контрол на химичния състав:
C | Si | Mn | P | S | Cu | |
Първата пещ | 3.7-3.9 | 0.6-0.75 | 0.1-0.25 | <0.05 | <0.02 |
Приемане на план за лечение със сфероидизираща инокулация: насочете 500 кг желязо към смесителя, вграден 1.2% нодлайзер Elkem, 0.8-1.0% покриващ агент и 0.4% стъклен стъклен камък в сфероидизиращата торба и директно желязо към торбата за нодулиране. Поставете 0.5% инокулант Elkem. След като процесът на сфероидизация приключи, поставете поточния инокулант на Elkem върху вътрешната повърхност на торбата, разбийте го напълно и използвайте EPIC инструмент за вземане на проби за анализ и тестване.
500 кг желязо може да се докосне директно към смесителя и 0.95% нискомагнезиев сфероидизиращ агент Elkem, 0.65% покриващ агент Elkem, 0.2% стоманен скрап и 0.1% препарат за отстраняване на шлаката са вградени в сфероидизиращата торбичка, а желязото може да се почука директно към сфероидизиращ пакет. След като сфероидизацията приключи, последващият инокулант на Elkem се поръсва върху повърхността, напълно се натрошава и пробата се анализира и тества с EPIC инструмент. Докоснете директно 500 кг желязо към сместа и сфероидизиращата торба е вградена с 1.2% нодлайзер Elkem, 0.3% покриващ агент, 0.2% инокулант Elkem, 0.5% стоманен скрап и 0.1% препарат за отстраняване на шлака, директно навън с желязо в сфероидизиращата торба и в същото време поставете 0.35% от инокуланта на Elkem.
След като сфероидизацията приключи, последващият инокулант на Elkem се поръсва върху повърхността, напълно се натрошава и пробата се анализира и тества с EPIC инструмент. Третият план е съотношението на таксата: 65% чугун, 35% скрап; контрол на химичния състав:
C | Si | Mn | P | S | Cu | |
Първата пещ | 3.8-4.0 | 1.1-1.4 | 0.1-0.25 | <0.05 | <0.02 |
Приема се планът за третиране с инокулиране със сфероидизация: 500 кг желязо се докосва директно към сместа, 1.2% нискомагнезиев сфероидизиращ агент Elkem, 0.8% покриващ агент и 0.1% препарат за отстраняване на шлаката са вградени в сфероидизиращата торба, а желязото се докосва директно към сфероидизираща торба. В същото време, 0.55% от инокуланта Elkem е бил поставен в него. След като процесът на сфероидизация приключи, поточният инокулант на Elkem беше поставен върху вътрешната повърхност на торбата, която беше напълно разбита, а пробите бяха анализирани и тествани с EPIC инструмент. Докоснете директно 500 кг желязо към смесителя, вграден 1.2% нискомагнезиев сфероидизиращ агент Elkem, 0.8% покриващ агент Elkem и 0.1% препарат за отстраняване на шлаки в сфероидизиращата торба, директно потупване на желязо към сфероидизиращата торба и в същото време инвестирайте 0.55 % Инокулант Elkem. След завършване на сфероидизацията, последващият инокулант на Elkem, поръсен върху повърхността, се разбива напълно, а пробата се анализира и тества с EPIC инструмент. Докоснете директно 500 кг желязо към сместа и предварително вградете 1.2% нискомагнезиев сфероидизиращ агент Elkem, 0.3% покриващ агент, 0.2% инокулант Elkem и 0.1% препарат за отстраняване на шлаки в сфероидизиращата торба, директно докосване на желязото до сфероидизиращия пакет, докато поставяте в 0.35% инокулант Elkem. След завършване на сфероидизацията, инокулантът Elkem, поръсен върху повърхността, се разбива напълно, а пробата се анализира и тества с EPIC инструмент. Експериментални методи за откриване и методи за анализ Съдържанието на въглерод и сяра в разтопеното желязо се открива чрез детектор за въглерод и сяра, а съдържанието на сплави като P, Mn и Cu се открива чрез анализатор на спектъра; кривата на охлаждане на различни химични състави пред пещта се открива от оборудването на Elkem EPIC. Например LET (температура на преход в течна фаза), CE (действителен въглероден еквивалент), G1, G2 и G3 имат различни стойности на интервалите. Резултати от теста и обсъждане Резултати и обсъждане на първата схема:
C | Si | Mn | P | S | Cu | |
1-1 | 3.40 | 2.51 | 0.20 | <0.05 | 0.007 | 0.14 |
1-2 | 3.45 | 1.90 | 0.18 | <0.05 | 0.010 | 0.14 |
1-3 | 3.30 | 2.61 | 0.18 | <0.05 | 0.013 | 0.14 |
Според различните методи на обработка, откритите EPIC изображения са както следва:
Крива 1: Кривата на първата проба от устата на разтопена желязна пепел от първата пещ
Крива 2: Кривата на резултатите от първата програма за пещ А
Крива 3: кривата на резултатите от първата схема на пещта В Крива 4: кривата на резултата от първата схема на пещ С
- ① От криви 1 и 2 можем да видим, че LET стойността на първата схема на пещ А се увеличава след процеса на сфероидизация, което показва, че нейната течна фаза Линейната температура се увеличава, но интервалът G1 е все още относително голям при 34%, а LET -ST времето за утаяване на графит е 115 секунди. В комбинация с химичния му състав е известно, че въглеродният му еквивалент е най -високият от трите разтвора в първата пещ.
- ②От криви 1 и 3 можем да видим, че стойността на LET се увеличава от 1132 на 1146 ° C, интервалът G1 е 36%, а времето за утаяване на графита LET-ST е 129 секунди. В комбинация с неговия химичен състав, ние знаем, че неговият въглероден еквивалент е първият Най -ниският от трите варианта в една пещ.
- ③ От криви 1 и 4 можем да видим, че когато стойността на LET се увеличи от 1132 на 1140, интервалът G1 е 32%. Времето за утаяване на LET-ST графит е 139 секунди, а неговият химичен състав въглероден еквивалент е средната стойност сред трите схеми на първата пещ.
- Колкото по-висока е стойността на LET, толкова по-висок е потенциалът за образуване на горещ метал, толкова по-ниска е склонността на белите уста към отливките при същите условия и толкова повече графитни топки; стойността LET-ST е времето за утаяване на графита. В процеса на производство на дебели и големи части тази стойност обикновено се изисква да бъде по -висока. Колкото по-голям, толкова по-добре, това означава, че графитът се утаява по време на целия процес на втвърдяване, което е полезно да се използва ефектът на саморазширяване на графита за компенсиране на частичното свиване; интервалът G1 е интервалът на утаяване на аустенит на разтопеното желязо. Колкото по -голям е G1, толкова по -голяма е склонността към свиване на желязото при свиване. Има два аспекта, които влияят върху стойността на G1. От една страна, това е ефектът на инокулация и способността за зародиш на разтопеното желязо, а от друга страна, въглеродният еквивалент на разтопеното желязо. Когато въглеродният еквивалент е същият, толкова по -добър е ефектът на инокулация, толкова по -ниска е стойността на G1 и по -малка е тенденцията за свиване.
- ⑤ Следователно изглежда, че в първата пещ след обработката на разтопено желязо вариант С е най -добрият, вариант В е вторият, а вариант А е най -лошият.
Резултати и обсъждане на втория вариант
C | Si | Mn | P | S | Cu | |
2-1 | 3.70 | 2.36 | 0.18 | <0.05 | 0.007 | - |
2-2 | 3.66 | 2.39 | 0.19 | <0.05 | 0.005 | - |
2-3 | 3.46 | 2.65 | 0.18 | <0.05 | 0.005 | - |
Според различните методи на обработка, откритите EPIC изображения са както следва:
Крива 5: Кривата на оригиналната проба от разтопена желязна пепел от втората пещ
Крива 6: Кривата на резултатите от втората програма за пещ А
Крива 7: Кривата на резултатите от втората програма за пещ В
Крива 8: Кривата на резултатите от втората програма за пещ C
- From От крива 5 и крива 6 може да се види, че стойността на LET е намалена от 1149 на 1141 ℃, интервалът G1 е 20%, а времето за утаяване на графита LET-ST е 146 секунди. В комбинация с химичния му състав е известно, че въглеродният му еквивалент е втората пещ. Най -високата от трите програми. След анализ по -ниската LET стойност на оригиналната крива на отвора на разтопена желязна пепел се дължи на добавянето на феросилиций и графитизиращ рекарбуризатор, което доведе до силна способност за незабавно нуклеиране на разтопено желязо.
- From От крива 5 и крива 7 може да се види, че стойността на LET е намалена от 1149 на 1139 ℃, интервалът G1 е 24%, а времето за утаяване на графита LET-ST е 146 секунди. В комбинация с химичния му състав е известно, че въглеродният му еквивалент е втората пещ. В средата на трите програми. Причината за намаляването на LET е същата като по -горе.
- From От крива 5 и крива 8 може да се види, че стойността на LET е намалена от 1149 на 1138 ° C, интервалът G1 е 33%, а времето за утаяване на графита LET-ST е 144 секунди. В комбинация с химичния му състав е известно, че въглеродният му еквивалент е втората пещ. Най -ниската от трите опции.
- ④ По принцип вторият план на пещта A с най -силна способност за зародиш има по -висока стойност LET, най -малката тенденция на свиване е също вторият план на пещта A, а стойността G1 е най -малката. Той показва, че увеличаването на стойността на СЕ може да намали тенденцията на свиване и да подобри способността за зародиш.
Резултати и обсъждане на третия вариант
C | Si | Mn | P | S | Cu | |
3-1 | 3.72 | 2.36 | 0.24 | <0.05 | 0.008 | - |
3-2 | 3.76 | 2.45 | 0.24 | <0.05 | 0.009 | - |
3-3 | 3.78 | 2.37 | 0.24 | <0.05 | 0.008 | - |
Крива 9: кривата на оригиналната проба от устата на разтопената желязна пепел на третата пещ
Крива 10: Кривата на резултатите от третата програма за пещ А
Крива 11: Кривата на резултатите от третия план на пещта B
Крива 12: Кривата на резултатите от третия план на пещта C
- ①От крива 9 и крива 10 може да се види, че стойността на LET е намалена от 1147 на 1145 ℃, стойността на G1 е 6%, LET-ST графит Времето за утаяване е 172.8 секунди, в комбинация с неговия химичен състав, известно е че неговият еквивалент на въглерод е най -ниският сред трите схеми на третата пещ.
- From От крива 9 и крива 11 може да се види, че стойността на LET намалява от 1147 на 1146 ° C, стойността на G1 е 10%, а времето за утаяване на графита LET-ST е 182.7 секунди. В комбинация с химичния му състав е известно, че въглеродният му еквивалент е третата пещ. Най -високата от трите програми.
- From От крива 9 и крива 10 може да се види, че стойността на LET е намалена от 1147 на 1146 ℃, стойността на G1 е 9%, а времето за утаяване на графита LET-ST е 194.4 секунди. В комбинация с химичния му състав е известно, че въглеродният му еквивалент е третата пещ. В средата на трите програми.
- ④Общата стойност на G1 на третия вариант е относително ниска, което показва, че стопеното желязо, разтопено по тази опция, има най -ниската склонност към свиване. Най -общо казано, разликата между трите черпака стопено желязо не е голяма. Относително казано, третият вариант на пещ А има най -добър ефект. Изводът от изпитването на пробата е да се използва подходящата еквивалентна на въглерод стойност за регулиране на съотношението на зареждане през разтопеното желязо на първата и втората пещи.
Стойността LET на първоначалното разтопено желязо на втората пещ е по -висока от тази на първата пещ, а стойността на G1 е по -малка от тази на първата пещ. Чрез регулиране на съотношението на зареждане на втората и третата пещи, замествайки чистия нискоманганов скрап с буца стомана, стойността на LET е близка, а стойността на G1 е значително намалена след пренабеляването. Следователно увеличаването на съдържанието на въглерод може да подобри способността за зародиш на оригиналното разтопено желязо и да намали.
Тенденцията към свиване има малки промени с вида на скрапа. Правилният процес на третиране със сфероидизираща инокулация се постига чрез сравняване на първия план А на пещта с плана В и плана С. Собственият сфероидизиращ агент и инокулант на фабриката възприемат съществуващия метод на третиране, а склонността към свиване и способността за зародиш на разтопеното желязо са по -добри. Бедни; Съгласно втория план на пещта А, план В и план В, когато дозата на сфероидизиращия агент е 1.2%, а дозата на инокуланта е 0.5, ефектът от обработката е най-добрият, а разликата между предварително вградения и подслушвания вход не е голяма; преминал Сравнявайки третите схеми на пещ A, B и C, няма очевидна разлика в ефектите от трите схеми за третиране.
Причината за промяната е CE стойността на оригиналното разтопено желязо. Накратко, с висока стойност на CE (C3.7-3.9, Si2.1-2.4), като се използва инокулант за нодулатор Elkem, доза на нодулизатор 1.2%, инокулант Elkem 0.5% и поток инокулант може да получи висока форма Разтопеното желязо с ядрена способност и тенденцията за ниско свиване улеснява получаването на отливки от ковък чугун, които отговарят на изискванията за качество. Заключения за приложение за производство Използвайте примерни заключения за изпитване за производството на дебелостенни части от ковък чугун. Планът е следният: тегло на топене 20 т, съотношение на зареждане чугун 65%, скрап стомана 35%, елкем нодулизатор 1.2%, инокулант елкем 0.5%+с инокулант Flow, оригиналното разтопено желязо C3.7-3.9, Si2.2- 2.5, Mn≤0.3, P≤0.05, S < 0.02, за производство, вземете изпитвателната лента за леене, прикрепена към отливката за тестване, и разчленете и наблюдавайте тялото на отливката. След дисекцията повърхността за обработка беше инспектирана и след обработката нямаше графитни плаващи и свиващи се дефекти и програмата беше успешна.
Да обобщим
- 1. Дебели стени от пластично желязо са трудни за контрол при производството на ковък чугун. Те имат характеристиките на голяма дебелина на стената, бавно охлаждане, съдържащо Mg и други елементи и висока склонност към свиване. Дефекти и скрап по време на производството могат лесно да възникнат, причинявайки икономически загуби. Специално за отливки от клас QT400-18AR, изискванията му за изпълнение: характеристики на опън Rm≥390; граница на текучест Re≥240; удължение A≥18; средна стойност на удара KV2≥14, минимална стойност на удара KV2≥11 и по -високи изисквания.
- 2. Чрез изпитване на процеса с малка проба, пробата за изливане на малка проба се тества за различни химични компоненти и различни методи на третиране с инокулиране със сфероидизация. EPIC оборудването на Elkem открива склонността към свиване на разтопеното желязо, определя подходящия химичен състав и правилния метод за третиране с инокулационна инокулация, и може да получи разтопеното желязо с най -малка тенденция на свиване.
- 3. Приложете данните, получени от тестовия процес с малка проба, към действителното производство, за да формирате ясен и стабилен производствен план за производството на дебелостенни части от ковано желязо. Чрез проверка на прикрепената тестова лента за леене и анатомично наблюдение на повърхността се установява, че планът е ефективен и отливката е произведена. Качеството е добро и отговаря на изискванията за качество.
Моля, запазете източника и адреса на тази статия за повторно отпечатване: Три вида схеми за топене и наливане на ковко желязо
Мингхе Компания за леене на умира са посветени на производството и осигуряват качествени и висококачествени части за леене (обхватът на части за леене на метали включва главно Тънкостенно леене под налягане,Топъл камер Die Casting,Студено камерно леене), Кръгло обслужване (услуга за леене под налягане,Cnc обработка,Изработка на плесени, Повърхностна обработка). Всички персонализирани алуминиеви отливки, леене с магнезий или Zamak / цинк и други отливки са добре дошли да се свържете с нас.
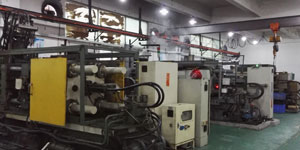
Под контрола на ISO9001 и TS 16949, всички процеси се извършват чрез стотици усъвършенствани машини за леене под налягане, 5-осни машини и други съоръжения, вариращи от бластери до Ultra Sonic перални машини. Minghe не само разполага с модерно оборудване, но и разполага с професионални екип от опитни инженери, оператори и инспектори, за да реализират дизайна на клиента.
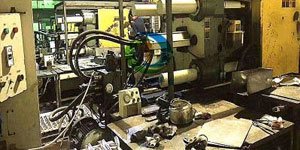
Договорен производител на отливки. Възможностите включват части за леене от алуминий със студена камера от 0.15 lbs. до 6 lbs., настройка за бърза смяна и обработка. Услугите с добавена стойност включват полиране, вибриране, отстраняване на обезкосмяването, струйно взривяване, боядисване, покритие, покритие, монтаж и обработка на инструменти. Материалите, с които се работи, включват сплави като 360, 380, 383 и 413.
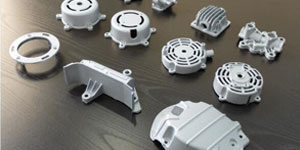
Помощ при проектиране на леене на цинк при съпътстващи инженерни услуги Персонализиран производител на прецизни отливки от цинкова матрица. Могат да се произвеждат миниатюрни отливки, отливки под високо налягане, отливки с многоплъзгащи се форми, конвенционални отливки за форми, единични матрици и независими отливки и отливки с кухина Отливките могат да се произвеждат с дължина и ширина до 24 инча в толеранс +/- 0.0005 инча.
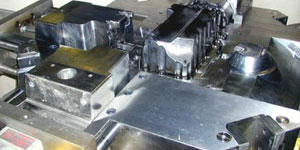
ISO 9001: 2015 сертифициран производител на магнезиево леене под налягане, Възможностите включват магнезиево леене под високо налягане до 200 тона гореща камера и 3000 тона студена камера, дизайн на инструментите, полиране, формоване, обработка, боядисване на прах и течности, пълен QA с CMM възможности , монтаж, опаковане и доставка.
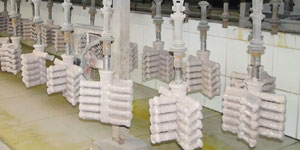
Сертифициран по ITAF16949 Включва допълнителна услуга за кастинг инвестиционно леене,пясъчно леене,Гравитационен кастинг, Изливане на пяна леене,Центробежно леене,Вакуумно леене,Постоянно леене на мухъл, .Възможностите включват EDI, инженерна помощ, солидно моделиране и вторична обработка.
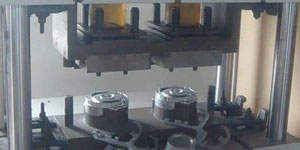
Кастинг индустрии Казуси за части за автомобили: Мотори, Самолети, Музикални инструменти, Водни плавателни съдове, Оптични устройства, Сензори, Модели, Електронни устройства, Кутии, Часовници, Машини, Двигатели, Мебели, Бижута, Конзоли, Телеком, Осветление, Медицински изделия, Фотографски устройства, Роботи, скулптури, озвучителна техника, спортна екипировка, инструментална екипировка, играчки и др.
Какво можем да ви помогнем да направите по-нататък?
∇ Отидете на началната страница за Китай за леене под налягане
→Части за леене-Разберете какво сме направили.
→ Съпоставени съвети за Услуги за леене под налягане
By Производител на леене под налягане Minghe | Категории: Полезни статии |Материал Tags: Алуминиево леене, Цинково леене, Магнезиево леене, Титаново леене, Леене от неръждаема стомана, Месинг леене,Бронзово леене,Кастинг на видео,История на компанията,Алуминиево леене под налягане | Коментарите са изключени