Високоякостна технология за топене на сив чугун
Тази статия представя как да се получи технология за топене на силен чугун с висока якост при условията на по-висок еквивалент на въглерод и по-добри изисквания за обработка в процеса на топене на електрически пещи и как да се контролират микроелементите на материала.
Ключови думи: сив чугун, въглероден еквивалент, механични свойства, обработващи свойства, микроелементи
Традиционната посока на управление на топенето на сив чугун е нисковъглероден високоякостен чугун (C: 2.7 ~ 3.0, Si: 2.0 ~ 2.3, Mn: 0.9 ~ 1.3). Въпреки че такива материали могат да отговарят на изискванията за механични свойства на материала, тяхното отливане и обработка Производителността е лоша. С развитието и разширяването на пазара на компанията, все повече и повече леярски продукти с висока трудност и високи технически изисквания за качество са включени в производствената последователност на MINGHE, особено когато MINGHE използва процеса на топене на електрически пещи с мощност, за да замени процеса на топене на куполи.
Получаването на високоефективен чугун с високо съдържание на въглерод при условия на топене в електрически пещи, за да се изпълнят изискванията на поръчките на клиентите, беше тема на изследване по това време. Тази статия описва технологията на производство на високоякостен сив чугун при условия на топене в електрически пещи.
Факторите, влияещи върху производителността на материалите
1.1 Влиянието на въглеродния еквивалент върху свойствата на материала
Основните фактори, които определят свойствата на сивия чугун, са графитната морфология и свойствата на металната матрица. Когато въглеродният еквивалент (CE = C+1/3Si) е висок, количеството графит се увеличава и формата на графита се влошава, когато условията на инкубация не са добри или има следи от вредни елементи. Такъв графит намалява ефективната площ на металната матрица, която може да понесе натоварването, и предизвиква концентрация на напрежение при понасяне на товара, така че здравината на металната матрица не може да се използва нормално, като по този начин се намалява здравината на чугуна. Сред материалите перлитът има добра якост и твърдост, докато феритът има по -мека основа и по -ниска якост. С увеличаването на количеството C и Si количеството на перлита ще намалява и количеството на ферита ще се увеличава. Следователно увеличаването на въглеродния еквивалент ще повлияе на якостта на опън на чугунените отливки и твърдостта на отливката във формата на графит и структурата на матрицата. При контрола на процеса на топене, контролът на въглеродния еквивалент е много важен фактор за решаване на характеристиките на материала.
1.2 Влиянието на легиращите елементи върху свойствата на материала
Легиращите елементи в сив чугун се отнасят главно до Mn, Cr, Cu, Sn, Mo и други елементи, които насърчават образуването на перлит. Съдържанието на тези елементи ще повлияе пряко върху съдържанието на перлит. В същото време, поради добавянето на легиращи елементи, той се усъвършенства до известна степен. Добавянето на графит намалява или дори изчезва количеството ферит в матрицата, докато перлитът се рафинира до известна степен, а феритът в него е твърд разтвор, подсилен поради определено количество легиращи елементи, така че чугунът винаги има по -висока производителност на якост. При контрола на процеса на топене, контролът на сплавта също е важно средство.
1.3 Влиянието на коефициента на заряд върху материалите
В миналото винаги сме настоявали, че докато химичният състав отговаря на изискванията на спецификацията, трябва да можем да получим изглед, който отговаря на стандартните механични свойства на материала, но всъщност този изглед вижда само конвенционалния химикал състав, и игнорира някои легиращи елементи и вредни елементи в него. Ролята на. Например чугунът е основният източник на Ti, така че използваното количество чугун ще повлияе пряко върху съдържанието на Ti в материала и ще окаже голямо влияние върху механичните свойства на материала. По същия начин скрап стомана е източник на много легиращи елементи, така че количеството скрап има много пряк ефект върху механичните свойства на чугуна. В първите дни, когато електрическата пещ беше пусната в употреба, винаги използвахме съотношението на зареждане на куполната пещ (чугун: 25 ~ 35%, скрап стомана: 30 ~ 35%). В резултат на това механичните свойства (якост на опън) на материала бяха много ниски. Когато количеството на използваната стомана оказва влияние върху производителността на чугуна, след регулиране на количеството скрап във времето, проблемът се решава бързо. Следователно скрапът е много важен контролен параметър в процеса на контрол на топенето. Следователно съотношението на заряда има пряко въздействие върху механичните свойства на чугунените материали и е в центъра на контрола на топенето.
1.4 Влиянието на микроелементите върху свойствата на материала
В миналото ние обръщахме внимание само на влиянието на общоприетите пет основни елемента върху качеството на чугуна по време на процеса на топене, докато ефектът на други микроелементи беше само качествено разбиране, но те рядко бяха анализирани и обсъждани количествено. През последните години, поради въздействието на технологията за леене Progress, топилното оборудване непрекъснато се актуализира, а куполите постепенно се заменят с електрически пещи. Въпреки че топенето на електрически пещи има своите несравними предимства при топенето на куполи, топенето на електрически пещи също губи някои от предимствата на топенето на куполи, така че влиянието на някои микроелементи върху чугуна също се отразява. Тъй като металургичната реакция в купола е много силна, зарядът е в силна окислителна атмосфера, по -голямата част от нея се окислява и се изхвърля със шлаката, само малка част ще остане в разтопеното желязо, така че някои имат неблагоприятен ефект върху леене Чрез металургичния процес на купола микроелементите обикновено нямат неблагоприятен ефект върху чугуна. По време на процеса на топене на купола, част от азота в кокса и азота (N2) във въздуха се разтварят в разтопеното желязо под формата на атоми при високи температури, което прави съдържанието на азот в разтопеното желязо относително високо.
Според статистиката, откакто електрическата пещ е пусната в експлоатация, отпадъчните продукти, причинени от високо съдържание на олово и бракувано разтопено желязо, тъй като съдържанието на олово е твърде високо, за да се регулира, са не по -малко от 100 тона, а броят на неквалифицираните продукти се дължи до недостатъчно съдържание на азот също беше доста високо, причинявайки на компанията големи икономически загуби.
Въз основа на нашия дългогодишен опит и теория в топенето на електрически пещи, аз вярвам, че ключовите микроелементи в процеса на топене на електрически пещи са предимно N, Pb и Ti. Ефектите на тези елементи върху сивия чугун са главно следните:
Олово
Когато съдържанието на олово в разтопеното желязо е високо (> 20PPm), особено при взаимодействие с по -високо съдържание на водород, е лесно да се образува графит Widmanstatten в отливки с дебели секции. Това е така, защото смолният пясък има добри топлоизолационни свойства и разтопеното желязо Охлаждането е по -бавно във формата, (тази тенденция е по -очевидна за дебели участъци), разтопеното желязо остава в течно състояние за по -дълго време и втвърдяването на разтопеното желязо е по -близо до състоянието на втвърдяване в равновесно състояние поради действието на олово и водород. Когато този вид леене се втвърди и продължи да се охлажда, въглеродът в аустенита ще се утаи и ще стане вторичен графит в твърдо състояние. При нормални обстоятелства вторичният графит само сгъстява евтектичните графитни люспи, което няма да окаже голямо влияние върху механичните свойства. Въпреки това, когато съдържанието на азот и водород е високо, повърхностната енергия на графита в същата фиксирана кристална равнина на аустенита ще бъде намалена, а вторичният графит ще расте нагоре по определена кристална равнина от аустенит и ще се простира в металната матрица. Наблюдавайте под микроскоп. Много малки графитни люспи, наподобяващи грапавини, растат отстрани на графитните люспи, известни като графитни власинки, което е причината за образуването на графит на Уидман. Алуминият в чугуна може да стимулира течното желязо да абсорбира водород и да увеличи неговото съдържание на водород. Следователно, алуминият също има косвен ефект върху образуването на графит Widmanstatten.
Когато графитът Widmanstatten се появи в чугун, неговите механични свойства са силно засегнати, особено якостта и твърдостта, които могат да бъдат намалени с около 50% в тежки случаи.
Графитът на Widman има следните металографски характеристики:
- 1) На 100-кратната фотомикрография има много малки, подобни на трън графитни люспи, прикрепени към грубата графитна люспица, която е графит Widmanstatten.
- 2) Връзката на обикновения кристален графит е свързана помежду си.
- 3) Когато графитната мрежа на Widmanstatten се разшири в матрицата при стайна температура, тя става крехката повърхност на матрицата, което значително ще намали механичните свойства на сивия чугун. Но от напречното сечение пукнатините на счупване все още се простират по графита, подобен на съвместно чип.
Азот
Подходящото количество азот може да стимулира образуването на графит, да стабилизира перлита, да подобри структурата на сивия чугун и да подобри работата на сивия чугун.
Азотът има две основни влияния върху сивия чугун. Едното е влиянието върху формата на графита, а другото е влиянието върху структурата на матрицата. Ефектът на азота върху графитната морфология е много сложен процес. Най -вече се проявява в: влиянието на адсорбционния слой върху графитната повърхност и влиянието на размера на евтектичната група. Тъй като азотът е почти неразтворим в графит, азотът непрекъснато се адсорбира отпред на растежа на графита и от двете страни на графита по време на процеса на евтектично втвърдяване, което води до увеличаване на околната концентрация на графит по време на процеса на утаяване, особено когато графитът се простира в разтопено желязо. На върха, той влияе върху растежа на графит на границата между течност и твърдо вещество. По време на процеса на евтектичен растеж има значителна разлика в разпределението на концентрацията на азот на върха и от двете страни на графитния лист. Адсорбционният слой от азотни атоми върху графитната повърхност може да възпрепятства дифузията на въглеродните атоми към графитната повърхност. Когато концентрацията на азот на фронта на графита е по -висока от тази на двете страни, скоростта на растеж на графита в надлъжна посока се намалява. За разлика от това, страничният растеж става по -лесен и в резултат графитът става по -къс и по -дебел. В същото време, тъй като винаги има дефекти в процеса на растеж на графита, част от азотните атоми се адсорбират на мястото на дефекта и не могат да дифундират, а границата на зърната ще бъде асиметрично наклонена в предната част на графитния растеж, а почивката все още ще расте в първоначалната посока. Графитът произвежда клони, а увеличаването на графитните клони е друга причина, поради която графитът става по -къс. По този начин, поради усъвършенстването на графитната структура, ефектът на разцепване върху структурата на матрицата се намалява, което благоприятства подобряването на характеристиките на чугуна.
Ефектът на азота върху структурата на матрицата е, че той е перлитен стабилизиращ елемент. Увеличаването на съдържанието на азот намалява температурата на евтектоидната трансформация на чугуна. Следователно, когато определено количество азот се съдържа в сив чугун, степента на преохлаждане на евтектоидната трансформация може да се увеличи, като по този начин се рафинира перлитът. От друга страна, тъй като атомният радиус на азота е по -малък от този на въглерода и желязото, той може да се използва като интерстициални атоми за разтваряне във ферит и цементит, което води до изкривяване на кристалната му решетка. Поради горните две причини, азотът може да има укрепващ ефект върху матрицата.
Въпреки че азотът може да подобри работата на сивия чугун, когато той надвишава определено количество, азотните пори и микропукнатини ще бъдат генерирани, както е показано на фигура 2, така че контролът на азота трябва да се контролира в определен диапазон. Обикновено 70-120PPm, когато надвишава 180PPm, производителността на чугуна ще падне рязко.
Ti е вреден елемент в чугуна. Причината е, че титанът има силен афинитет към азота. Когато съдържанието на титан в сив чугун е високо, това не е от полза за укрепващия ефект на азота. Първо, той образува TiN съединение с азот, което намалява Всъщност, точно защото този свободен азот има ефект на укрепване на твърдия разтвор върху сив чугун. Следователно нивото на съдържание на титан косвено влияе върху работата на сивия чугун.
Технология за управление на топенето
2.1 Избор на химичен състав на материала
Чрез горния анализ контролът на химичния състав е много важен в технологията на топене и е в основата на контрола на топенето. Следователно разумният химичен състав е основата за осигуряване на експлоатационните характеристики на материала. Обикновено контролът на състава на чугун с висока якост (якост на опън ≥300N/mm2) включва главно и т.н. C, Si, Mn, P, S, Cu, Cr, Pb, N
2.3 Контролна технология на микроелементите
В действителния контрол на процеса, въз основа на анализа на заряда, се потвърждава, че източникът на олово е основно скрап стомана. Следователно контролът на оловото в суровината е главно да се контролират включванията на Pb в стоманената скрап, а съдържанието на олово обикновено се контролира под 15 ppm. Ако съдържанието на олово в суровото разтопено желязо е> 20 ppm, по време на инкубационното третиране трябва да се извърши специално третиране на влошаване.
Тъй като Ti се получава главно от чугун, контролът върху Ti е главно за контрол на чугуна. От една страна, при закупуването е необходимо да се поставят строги изисквания за съдържанието на Ti в чугун. Обикновено съдържанието на титан в чугун се изисква да бъде: Ti <0.8%, а другият Един аспект е да се коригира количеството на използване във времето според съдържанието на титан в чугуна.
Основно идва от материали за пренабеляване и скрап стомана, така че контролът на N е главно за контрол на материалите за пренабеляване и скрап стомана. Както бе споменато по -горе, твърде ниските и твърде високите имат отрицателна страна за работата на сивия чугун, така че съдържанието на N Обхватът на контрол обикновено е: 70 ~ 120 ppm, но съдържанието на N трябва да има разумно съответствие с съдържание на Ti. Като цяло връзката между N и Ti е: N: Ti = 1: 3.42, тоест 0.01% от Ti може да абсорбира 30PPm азот. Общото препоръчително количество азот по време на производството е: N = 0.006 ~ 0.01+Ti/3.42.
2.4 Контролна технология на процеса на топене
1) Технология на инокулация
Целта на инокулационното лечение е да се насърчи графитизацията, да се намали склонността към бяла уста и да се намали чувствителността на крайната повърхност; контролират морфологията на графита и премахват недоохладения графит; подходящо увеличаване на броя на евтектичните клъстери и насърчаване на образуването на люспен перлит, така че да се подобрят якостните характеристики на чугуна и други цели за изпълнение.
Влиянието на температурата на разтопеното желязо върху инокулацията и контролирането на температурата на разтопеното желязо оказват значително влияние върху инокулацията. Увеличаването на температурата на прегряване на разтопеното желязо в определени граници и поддържането му за определен период от време може да накара неразтворените графитни частици да останат в разтопеното желязо, което може да бъде напълно разтворено в разтопеното желязо, за да се елиминира генетичното влияние на чугуна и придават пълна сила на инокулиращия ефект на инокуланта, подобряват способността за плодовитост на разтопеното желязо. При контрола на процеса температурата на прегряване се увеличава до 1500 ~ 1520 ℃, а температурата на инокулация се контролира при 1420 ~ 1450 ℃.
Размерът на частиците на инокуланта е важен индикатор за състоянието на инокуланта и има голямо влияние върху ефекта на инокуланта. Ако размерът на частиците е твърде фин, лесно е да се разпръсне или да се окисли в разтопената шлака и да загуби ефекта си. Ако размерът на частиците е твърде голям, инокулантът няма да се стопи или разтвори напълно. Той не само не може да прояви напълно своя инокулиращ ефект, но и ще причини сегрегация, твърди петна, преохладен графит и други дефекти. Следователно размерът на частиците на инокуланта трябва да се контролира в рамките на 2 ~ 5 mm, доколкото е възможно. Осигурете инкубационния ефект.
При контрола на процеса процесът на инокулиране се инокулира главно в инкубационния резервоар, така че изливането на пакет от отливки може основно да приключи преди инкубацията да намалее. Но за относително големи части и части, отливани с двоен черпак, той не може да отговаря на изискванията. Поради това се възприема методът на късната инокулация: т.е. инокулацията с плаващ силиций се извършва в черпака преди изливането на отливката (количеството на инокулацията е 0.1%), което намалява или не съществува спад на инокулацията и подобрява ефекта от инокулацията.
2) Легиращо третиране
Легиращата обработка добавя малко количество легиращи елементи към обикновения чугун за подобряване на механичните свойства на сивия чугун. При контрола на процеса на топене добавянето на сплави е предимно за частите, които клиентите изискват да бъдат закалени, и частите със сравнително дебели направляващи релси, основните добавени елементи от сплав и количеството на добавяне.
Това гарантира до известна степен намаляването на производителността поради увеличаването на стойността на CE, а за закалените части се подобрява втвърдяването по време на закаляването. Осигурете дълбочината на закаляване.
По време на процеса на подаване и топене редът на подаване на ключовия контрол на този етап е да се подава скрап стомана, механично желязо и чугун в ред на приоритет. За да се намалят загубите от изгаряне на легиращите елементи, феросплавта трябва да се добави в края. Когато студеният материал е напълно изчистен, температурата се повишава до 1450 ℃. Това е точка А. Ако е по -ниска от 1450 ° C, съществува риск от непълно разтваряне на рекарбуризатора или феросплавта.
В параграфи АБ следва да се извършат следните лечения:
- Измерване на температурата;
- Шлака за пречистване;
- Вземане на проби и анализ на химичния състав;
- Анализирайте конвенционалните елементи и микроелементите с термичен спектрометър;
- Вземете тестовия образец на триъгълника, за да измерите стойността на CW;
- След регулиране на разтопеното желязо според различни резултати от теста, продължете да подавате захранване за 10 минути и след това повторно вземете проба и анализирайте. След като потвърдите, че всички данни са нормални, продължете да повишавате температурата до около 1500 ° C, тоест точка C. В секцията CD оставете разтопеното желязо да престои 5 до 10 минути и след това вземете триъгълна проба, за да тествате CW стойност. След измерване на температурата, подгответе ютията за потупване.
Контрол на триъгълна проба
За различни степени, определете контролния диапазон на бялата уста (CW) на различни триъгълни тестови блокове и определете качеството на разтопеното желязо в комбинация с анализа на състава пред пещта.
Заключение
Посочената по-горе технология за топене на сив чугун се прилага успешно в CSMF в продължение на 8 години от 1996 до 2003 г. CE на отливките се контролира в съответствие с предположението от 3.6 ~ 3.9, независимо дали става въпрос за индекса на якост на опън или индекса на физическата твърдост ( особено част от Твърдостта на направляващата релса на частите на металорежещите машини отговаря на изискванията, което значително подобрява характеристиките на рязане на отливката. Доказано е, че тази технология е финализирана технология и нейните контролни точки са както следва:
- 3.1 Контрол на химичния състав на материалите
- 3.2 Определяне на съотношението на заряда
- 3.3 Контролна технология на микроелементите
- 3.4 Контрол на процеса на третиране с инокулация
- 3.5 Легиране с легиране
- 3.6 Температурен контрол на процеса на топене
- 3.7 Контрол на триъгълник
Моля, запазете източника и адреса на тази статия за повторно отпечатване: Високоякостна технология за топене на сив чугун
Мингхе Компания за леене на умира са посветени на производството и осигуряват качествени и висококачествени части за леене (обхватът на части за леене на метали включва главно Тънкостенно леене под налягане,Топъл камер Die Casting,Студено камерно леене), Кръгло обслужване (услуга за леене под налягане,Cnc обработка,Изработка на плесени, Повърхностна обработка). Всички персонализирани алуминиеви отливки, леене с магнезий или Zamak / цинк и други отливки са добре дошли да се свържете с нас.
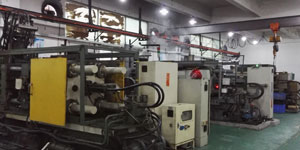
Под контрола на ISO9001 и TS 16949, всички процеси се извършват чрез стотици усъвършенствани машини за леене под налягане, 5-осни машини и други съоръжения, вариращи от бластери до Ultra Sonic перални машини. Minghe не само разполага с модерно оборудване, но и разполага с професионални екип от опитни инженери, оператори и инспектори, за да реализират дизайна на клиента.
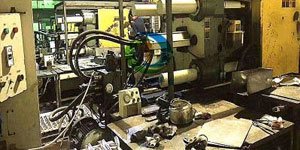
Договорен производител на отливки. Възможностите включват части за леене от алуминий със студена камера от 0.15 lbs. до 6 lbs., настройка за бърза смяна и обработка. Услугите с добавена стойност включват полиране, вибриране, отстраняване на обезкосмяването, струйно взривяване, боядисване, покритие, покритие, монтаж и обработка на инструменти. Материалите, с които се работи, включват сплави като 360, 380, 383 и 413.
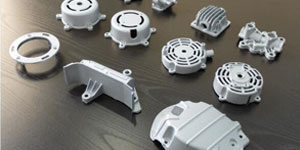
Помощ при проектиране на леене на цинк при съпътстващи инженерни услуги Персонализиран производител на прецизни отливки от цинкова матрица. Могат да се произвеждат миниатюрни отливки, отливки под високо налягане, отливки с многоплъзгащи се форми, конвенционални отливки за форми, единични матрици и независими отливки и отливки с кухина Отливките могат да се произвеждат с дължина и ширина до 24 инча в толеранс +/- 0.0005 инча.
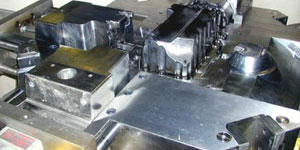
ISO 9001: 2015 сертифициран производител на магнезиево леене под налягане, Възможностите включват магнезиево леене под високо налягане до 200 тона гореща камера и 3000 тона студена камера, дизайн на инструментите, полиране, формоване, обработка, боядисване на прах и течности, пълен QA с CMM възможности , монтаж, опаковане и доставка.
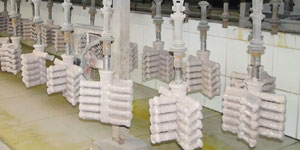
Сертифициран по ITAF16949 Включва допълнителна услуга за кастинг инвестиционно леене,пясъчно леене,Гравитационен кастинг, Изливане на пяна леене,Центробежно леене,Вакуумно леене,Постоянно леене на мухъл, .Възможностите включват EDI, инженерна помощ, солидно моделиране и вторична обработка.
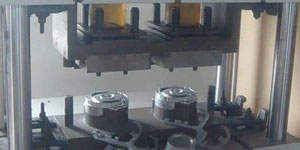
Кастинг индустрии Казуси за части за автомобили: Мотори, Самолети, Музикални инструменти, Водни плавателни съдове, Оптични устройства, Сензори, Модели, Електронни устройства, Кутии, Часовници, Машини, Двигатели, Мебели, Бижута, Конзоли, Телеком, Осветление, Медицински изделия, Фотографски устройства, Роботи, скулптури, озвучителна техника, спортна екипировка, инструментална екипировка, играчки и др.
Какво можем да ви помогнем да направите по-нататък?
∇ Отидете на началната страница за Китай за леене под налягане
→Части за леене-Разберете какво сме направили.
→ Съпоставени съвети за Услуги за леене под налягане
By Производител на леене под налягане Minghe | Категории: Полезни статии |Материал Tags: Алуминиево леене, Цинково леене, Магнезиево леене, Титаново леене, Леене от неръждаема стомана, Месинг леене,Бронзово леене,Кастинг на видео,История на компанията,Алуминиево леене под налягане | Коментарите са изключени