Различни фактори, влияещи върху стабилността на размерите на инвестиционните отливки
Постоянното подобряване на точността на размерите на инвестиционните отливки и намаляването на отпадъчните продукти, причинени от извънгабаритни размери, винаги е била една от основните цели, преследвани от работниците за леене на инвестиции у нас и в чужбина.
1. Стабилност на размерите на отливките за инвестиции
1. Стабилност на размерите на восъчния модел и неговите влияещи фактори
В повечето случаи размерът на восъчната форма се колебае значително, когато размерът на отливката се колебае, и има няколко изключения. Като цяло колебанията в размера на восъчната форма представляват 10% до 70% от колебанието в размера на отливката.
Параметрите на процеса на формоване оказват решаващо влияние върху стабилността на размерите на восъчната форма. Основните фактори са както следва:
(1) Температура на пресоване на восък
Различните формовъчни материали имат различни характеристики поради влиянието на температурата на пресоване на восък. Когато се използват формовъчни материали на восъчна основа, температурата на пресоване на восък е много чувствителна към влиянието на стабилността на размерите на восъчната форма, докато формовочните материали на смола имат по-малко влияние.
(2) Инжекционно налягане
Когато налягането е малко, скоростта на свиване на восъчната форма намалява значително с увеличаване на налягането. Въпреки това, след като налягането се увеличи до известна степен (≥1.6MPa), налягането няма почти никакъв ефект върху размера на восъчната форма. Не е чудно, че резултатите от чуждестранни тестове често заключават, че „натискът няма нищо общо с размера на восъчната форма“, но впечатлението на много местни компании не е съвсем същото.
(3) Дебит
Дебитът на материала за матрица може да се промени по следните два начина, но влиянието върху размера на восъчната форма не е същото:
· Чрез промяна на скоростта на потока на восъчната преса, този метод има малък ефект върху свиването на восъчната форма. Той обаче има важно влияние върху пълненето и качеството на повърхността на тънкостенни части със сложни форми или восъчни форми със сърцевини.
· Този метод оказва голямо влияние, като променя площта на напречното сечение на отвора за инжектиране на восък, тъй като увеличаването на площта на напречното сечение на отвора за инжектиране на восък може не само да намали температурата на пресоване на восък, но и да удължи втвърдяването времето на материала на формата в отвора за инжектиране на восък, като по този начин се увеличава уплътняването на восъчната форма Степента на свиване и повърхностното свиване се намаляват.
(4) Време за инжектиране
Така нареченото време за инжектиране тук включва три времеви периода на пълнене, уплътняване и поддръжка. Времето за пълнене се отнася до времето, през което формовъчният материал запълва формовъчната кухина; уплътняването се отнася до времето от пълнене на формоването до затваряне на дюзата за инжектиране на восък; и задържането се отнася до времето от затварянето на дюзата за инжектиране на восък до изхвърлянето на матрицата.
Времето на инжектиране оказва значително влияние върху скоростта на свиване на восъчната форма. Това се дължи на факта, че в кухината може да се изтласка повече матричен материал чрез увеличаване на времето за инжектиране, а восъчната форма ще бъде по -уплътнена, като по този начин ще се намали скоростта на свиване. Теглото на восъчния модел се увеличава с удълженото време на уплътняване. Времето за уплътняване трябва да е подходящо. Ако времето за уплътняване е твърде дълго, материалът на формата на отвора за инжектиране на восък е напълно втвърден и уплътняването няма да работи. От фигура 4 може да се види също, че когато времето за инжектиране е кратко (15-25s), температурата на пресоване на восък се повишава и скоростта на свиване се увеличава; но когато времето за инжектиране се удължи до 25-35s (при предпоставката, че времето за пълнене остава постоянно, действителното Горното е за удължаване на времето за уплътняване) Влиянието на температурата на пресоване на восък става по-малко; когато времето за инжектиране се увеличи до повече от 35 секунди, ще възникне обратната ситуация, тоест с повишаване на температурата на пресоване на восък, скоростта на свиване на восъчната форма ще намалее. Това явление може да се обясни с това, че повишаването на температурата на формата на материала и удължаването на времето за уплътняване имат същия ефект като увеличаването на степента на уплътняване на восъчна форма.
(5) Оборудване за температура на формоване и пресоване на восък
Температурата на формоване е висока, восъчната форма се охлажда бавно и скоростта на свиване се увеличава. Това е така, защото восъчната форма все още е в пресовото формоване, преди матрицата да бъде изхвърлена, а свиването е ограничено, но след като матрицата е изхвърлена, тя става свободна за свиване. Следователно, ако температурата на восъчната форма е висока, когато матрицата се освободи, крайната скорост на свиване ще бъде голяма и обратно, скоростта на свиване ще бъде малка.
По същия начин охлаждащата система на восъчната преса може да окаже влияние с около 0.3% върху размера на восъчната форма.
И накрая, заслужава да се подчертае, че когато се използват форми на восъчна основа, восъчната паста е трифазна система за съвместно съществуване на твърдо, течно и газообразно. Съотношението на обема между трите фази има голямо влияние върху размера на восъчната форма. Пропорционалната връзка между тези три не може да бъде контролирана в действителното производство, което също е важна причина за лошата стабилност на размерите на восъчните форми, използващи формовъчни материали на восъчна основа.
2. Влиянието на материала на корпуса и процеса на производство на корпуса върху стабилността на размерите на отливките
Влиянието на корпуса на формата върху размера на отливката се дължи главно на термичното разширение и термичната деформация (пълзене при висока температура) на корпуса на формата по време на изпичане и ограничаването (запушването) на корпуса на формата върху охлаждащото свиване на леене.
(1) Термично разширяване на черупката
Основно зависи от материала на корпуса. Различните огнеупорни материали имат различна скорост на разширяване. Сред често използваните огнеупорни материали, разтопеният силициев диоксид има най -малка степен на разширяване, следван от алуминиев силикат, а силициевият диоксид е най -големият и неравномерен. След изпитването е установено, че алуминиево -силикатната обвивка може да се нагрее от стайна температура до 1000 ℃, черупката може да произведе около 0.25% разширение, което представлява малка част от общото свиване на размера на отливката. Следователно, ако се използват такива огнеупорни материали, корпусът има по -добра стабилност на размерите, като например стопен силициев диоксид несъмнено ще бъде по -добър. Ако обаче се използва силициев диоксид, размерът на черупката варира значително.
(2) Термична деформация (пълзене при висока температура)
Например, черупка, използваща водно стъкло като свързващо вещество, има значително по -висока степен на пълзене при високи температури над 1000 ° C, отколкото тази на силициевия зол и етилсиликатните обвивки. Въпреки че самият разтопен корунд има висока огнеупорна способност, поради наличието на примеси като натриев оксид, температурата на изпичане на черупката по -висока от 1000 ℃ също може да причини пълзене, което води до лоша стабилност на размерите.
(3) Задържането на корпуса на мухъл върху свиването на отливката - отдръпването и сгъването на корпуса на матрицата Това също зависи главно от материала на корпуса на формата.
В обобщение, огнеупорните материали играят важна роля за влиянието на черупката върху колебанията в размера на отливката, но ролята на свързващото вещество не може да бъде пренебрегната. За разлика от това, въздействието на процеса на производство на черупки е малко.
3. Влиянието на напрежението, причинено от неравномерното охлаждане на отливките, върху стабилността на размерите
Скоростта на охлаждане на всяка част от отливката (включително решетъчната система) е различна, което генерира термично напрежение и деформира отливката, като по този начин влияе върху стабилността на размерите. Това често се среща в реалното производство. Намаляването на скоростта на охлаждане на отливките и подобряването на комбинацията от бегачи са ефективни превантивни мерки.
2. Ключът за подобряване на точността на свиване на матрицата е зададен правилно
Горепосочената "стабилност на размерите" е различна от "точност на размерите" и "прецизност (прецизност)". Стабилността на размерите (т.е. прецизността) е синоним на последователност на размерите, отразяваща степента на измерение на колебанията или дисперсията и обикновено се измерва със стандартното отклонение σ. Основната причина за нестабилността на размерите е слабото управление на процеса, което е случайна грешка. Точността се отнася до степента, в която средната аритметична стойност на много измерени стойности се отклонява от номиналния размер за определен размер върху отливката, тоест размера на средното отклонение. При инвестиционното леене основната причина за лошата точност на размерите е неправилното задаване на скоростта на свиване по време на профилирането, което е системна грешка, която обикновено се коригира чрез многократно поправяне на матрицата. Точността на размерите (прецизност) е комбинация от горните две. Следователно, за да се подобри точността на размерите на отливките и да се реши проблемът с допустимите отклонения на размера на продукта, не само процесът трябва да бъде строго контролиран, за да се намалят колебанията на размерите, но също така и скоростта на свиване на всяко измерение на отливката трябва да бъде правилно зададена при проектирането на профила .
Добре известно е, че крайното общо свиване на прецизните отливки е комбинация от восъчна форма, свиване на сплав и малко количество разширение на обвивката. Черупката набъбва с около 0.25%, а ефектът й е ограничен. Въпреки че скоростта на линейно свиване на сплавта често е по -голяма от тази на восъчната форма, колебанията в размерите, причинени от процеса на пресоване на восък, имат по -голямо въздействие. За да се намалят разходите за ремонт на мухъл и да се намалят колебанията в размера на отливката, е много важно да се контролира скоростта на свиване на восъчната форма.
1. Свиване на восъчна мухъл
Свиването на восъчната форма трябва да се измери, след като размерът на восъчната форма се стабилизира напълно. Това е така, защото свиването на восъчната форма не спира напълно след изхвърлянето на формата. Размерът на восъчната форма понякога се стабилизира само няколко дни след изхвърлянето на формата. Въпреки това, по -голямата част от свиването на матричния материал основно завършва в рамките на един до няколко часа след изхвърлянето на формата. Скоростта на свиване на восъчната мухъл има главно следните влияещи фактори:
(1) Вид на формата на формата;
(2) Размери на сечението на восъчен модел;
Струва си да се подчертае, че размерът на напречното сечение на восъчната форма има значителен ефект върху скоростта на свиване. Например скоростта на свиване на типичен незапълнен формовъчен материал при пресоване на восъчни форми с различна дебелина. Дебелината на сечението на восъчната форма обикновено не трябва да надвишава 13 мм. Когато дебелината е по-голяма от 13 мм, дебелината на стената може да бъде намалена чрез използване на студени восъчни блокове или метални сърцевини, за да се постигне целта за намаляване на свиването, което е особено важно за материали, които не са пълнежни.
Забележка: 1. Степента на свиване на водоразтворимия плесен е около 0.25%;
2. Когато се използват разтворими сърцевини, керамични ядра или кварцови стъклени тръби, няма линейно свиване на восъчната форма в контакт с сърцевината;
(3) Основни типове
Размерът на кухината на восъчната форма несъмнено е в съответствие с формата на сърцевината. Следователно използването на сърцевини се превърна в начин за подобряване на точността на размерите на кухината на восъчната форма.
2. Свиване на сплав
Свиването на сплавите зависи главно от следните фактори:
· Тип леяна сплав и химичен състав;
· Геометрия на леене (включително състояние на ограничение и размер на сечението);
· Параметри на леене, като температура на изливане, температура на корпуса, скорост на охлаждане на леене и др .;
· Използване на керамични сърцевини, кварцови стъклени тръби и др.
Тъй като температурата на изливане, температурата на обвивката, скоростта на охлаждане на леенето и други параметри на процеса обикновено се контролират стриктно от стандартните технологични карти по време на производствения процес, колебанията в размера, причинени от това, не са големи между различните производствени партиди. Дори ако температурата на изливане надвишава диапазона, изискван от спецификацията на процеса, колебанията в размера на отливката обикновено не са големи. Подобно на восъчната форма, размерът на сечението на отливката и ограниченията на черупката на матрицата са основните фактори, които влияят върху свиването на сплавта. Опитът показва, че скоростта на свиване на напълно ограничените размери е 85% до 89% от скоростта на свободно свиване; полуограниченият размер е 94% до 95%.
3. Минималният брой на първата партида проби за измерване
Степента на свиване, изброени по -горе, са емпирични данни, базирани на миналия опит, а не на реалната скорост на свиване. Проектиране и производство на форми според тези данни, ремонтът е неизбежен. За да се подобри точността и успеваемостта на ремонтите и да се намали броят на ремонтите, ключова връзка е внимателно да се провери размерът на достатъчен брой проби за пробно леене. Тъй като размерът на отливките, които произвеждаме, не може да бъде абсолютно еднакъв, така че само когато броят на измерените проби е достатъчно голям, средната получена стойност може да бъде близка до истинската средна аритметика. От това не е трудно да се види, че минималният брой измервателни проби е пряко свързан с технологичната способност на производствения процес да контролира консистенцията на размера на продукта (Process Capability). Ако отливките са напълно еднакви по размер, тогава е необходима само една проба за тестване; Обратно, ако размерът на отливката варира значително,
Необходимо е да се измерват много проби, за да се получат по -точни данни за свиване. Както бе споменато по -рано, способността на производствения процес да контролира размера може да бъде представена чрез 6σ от размера на отливката, произведен от този процес. От сегашното технологично ниво на повечето инвестиционни леярни, Hp е предимно над 0.5, така че първата партида измервателни проби обикновено изисква най -малко 11 проби.
три. Анализ на измервателната система
Когато анализираме и решаваме проблеми с размера на продукта, трябва да обърнем внимание на точността и надеждността на използваната измервателна система. В допълнение към честото калибриране на самите измервателни уреди и оборудване, също е важно да се сведат до минимум грешките при измерването. Ако измервателната система (включително оператора и метода на работа) има голяма грешка, не само отхвърлянията могат да бъдат оценени като квалифицирани продукти, но и много квалифицирани продукти могат да бъдат преценени погрешно като отхвърлени, като и двете могат да причинят големи аварии или ненужна икономическа загуби. Най -лесният начин да се определи дали измервателната система е подходяща за конкретна измервателна задача е да се извършат квалификационни тестове за възпроизводимост и повторяемост. Така наречената повторяемост означава, че един и същ инспектор използва един и същ инструмент (или оборудване) и метод, за да провери същата част и да получи последователността на резултатите. Възпроизводимостта се отнася до последователността на резултатите, получени от различни оператори, използващи различни инструменти за проверка на една и съща част. Американската група за действие в автомобилната индустрия (Група за действие в автомобилната индустрия) предвижда, че процентът на интегрираното стандартно отклонение на повторяемостта и възпроизводимостта на R&R в стандартното отклонение на измерените колебания в размера на отливките е ≤30% като стандарт за измервателната система, за да отговаря на изисквания [5]. При измерването на някои отливки с големи размери и сложна форма не всички измервателни системи могат да отговорят на това изискване. Допустимата грешка при измерване при измерване на форми трябва да бъде по -малка, обикновено 1/3.
четири. Структура на формата и ниво на обработка
Добре известно е, че структурата на формата и качеството на обработка имат важно влияние върху размера и геометрията на восъчната форма. Например, дали механизмът за позициониране и затягане е точен и надежден, дали подходящият хлабина на подвижните части (като подвижни блокове, болтове и т.н.) е подходящ, дали методът на изтегляне е от полза, за да се гарантира точността на размерите на отливките Излишно е да казвам, че за значителен брой местни предприятия за леене на инвестиции нивото на проектиране и производство на мухъл все още трябва спешно да се подобри.
Пет. в заключение
От горния анализ не е трудно да се види, че подобряването на точността на размерите на инвестиционните отливки е системен проект, включващ всички аспекти на производствения процес на леене на инвестиции. Основните моменти могат да бъдат обобщени, както следва:
1) Строго контролирайте параметрите на процеса на формоване, особено параметрите, които оказват значително влияние върху размера на отливката.
2) Изберете подходящия материал на обвивката.
3) Съберете, пребройте и анализирайте данни, свързани със свиването, по правилен метод, който отговаря на статистическите принципи, за да се подобри точността на разпределението на свиването.
4) Често наблюдавайте измервателната система (включително оборудване, инспекционен персонал и технология), за да се уверите, че грешките при повторяемост и възпроизводимост отговарят на посочените изисквания.
5) Постоянно подобряване на нивото на проектиране и производство на форми.
6) Мерки като корекция на леене и стабилизираща топлинна обработка все още са необходими в много случаи
Моля, запазете източника и адреса на тази статия за повторно отпечатване: Различни фактори, влияещи върху стабилността на размерите на инвестиционните отливки
Мингхе Компания за леене на умира са посветени на производството и осигуряват качествени и висококачествени части за леене (обхватът на части за леене на метали включва главно Тънкостенно леене под налягане,Топъл камер Die Casting,Студено камерно леене), Кръгло обслужване (услуга за леене под налягане,Cnc обработка,Изработка на плесени, Повърхностна обработка). Всички персонализирани алуминиеви отливки, леене с магнезий или Zamak / цинк и други отливки са добре дошли да се свържете с нас.
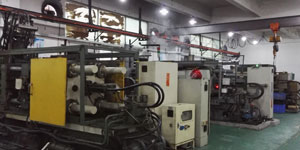
Под контрола на ISO9001 и TS 16949, всички процеси се извършват чрез стотици усъвършенствани машини за леене под налягане, 5-осни машини и други съоръжения, вариращи от бластери до Ultra Sonic перални машини. Minghe не само разполага с модерно оборудване, но и разполага с професионални екип от опитни инженери, оператори и инспектори, за да реализират дизайна на клиента.
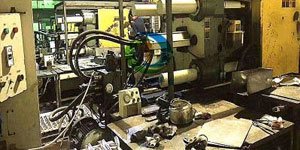
Договорен производител на отливки. Възможностите включват части за леене от алуминий със студена камера от 0.15 lbs. до 6 lbs., настройка за бърза смяна и обработка. Услугите с добавена стойност включват полиране, вибриране, отстраняване на обезкосмяването, струйно взривяване, боядисване, покритие, покритие, монтаж и обработка на инструменти. Материалите, с които се работи, включват сплави като 360, 380, 383 и 413.
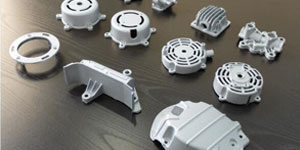
Помощ при проектиране на леене на цинк при съпътстващи инженерни услуги Персонализиран производител на прецизни отливки от цинкова матрица. Могат да се произвеждат миниатюрни отливки, отливки под високо налягане, отливки с многоплъзгащи се форми, конвенционални отливки за форми, единични матрици и независими отливки и отливки с кухина Отливките могат да се произвеждат с дължина и ширина до 24 инча в толеранс +/- 0.0005 инча.
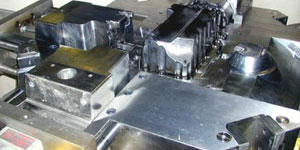
ISO 9001: 2015 сертифициран производител на магнезиево леене под налягане, Възможностите включват магнезиево леене под високо налягане до 200 тона гореща камера и 3000 тона студена камера, дизайн на инструментите, полиране, формоване, обработка, боядисване на прах и течности, пълен QA с CMM възможности , монтаж, опаковане и доставка.
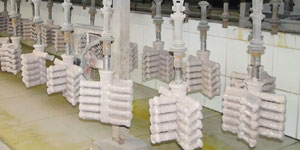
Сертифициран по ITAF16949 Включва допълнителна услуга за кастинг инвестиционно леене,пясъчно леене,Гравитационен кастинг, Изливане на пяна леене,Центробежно леене,Вакуумно леене,Постоянно леене на мухъл, .Възможностите включват EDI, инженерна помощ, солидно моделиране и вторична обработка.
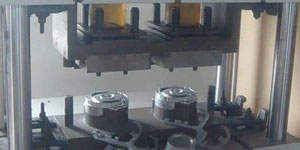
Кастинг индустрии Казуси за части за автомобили: Мотори, Самолети, Музикални инструменти, Водни плавателни съдове, Оптични устройства, Сензори, Модели, Електронни устройства, Кутии, Часовници, Машини, Двигатели, Мебели, Бижута, Конзоли, Телеком, Осветление, Медицински изделия, Фотографски устройства, Роботи, скулптури, озвучителна техника, спортна екипировка, инструментална екипировка, играчки и др.
Какво можем да ви помогнем да направите по-нататък?
∇ Отидете на началната страница за Китай за леене под налягане
→Части за леене-Разберете какво сме направили.
→ Съпоставени съвети за Услуги за леене под налягане
By Производител на леене под налягане Minghe | Категории: Полезни статии |Материал Tags: Алуминиево леене, Цинково леене, Магнезиево леене, Титаново леене, Леене от неръждаема стомана, Месинг леене,Бронзово леене,Кастинг на видео,История на компанията,Алуминиево леене под налягане | Коментарите са изключени