Процесният контрол на производството на вермикулярно желязо
В сравнение със сивото желязо, якостта на опън на вермикулярното желязо се увеличава с поне 70%, модулът на еластичност се увеличава с 35%, а якостта на умора се удвоява почти двойно. В сравнение с алуминиевата сплав, здравината и твърдостта на вермикулярното желязо са два пъти по -високи, а якостта на умора е два пъти по -висока. Тези характеристики на вермуларното желязо дават възможност на двигателя да подобри съотношението мощност/тегло и да увеличи налягането в цилиндъра. Увеличаването на налягането в цилиндъра е ключът към оптималната работа на следващото поколение дизелов двигател с директно впръскване. За да отговори на широкото приложение на вермикулярно желязо, леярската промишленост в момента се подготвя активно, инвестира големи средства и възстановява нови процеси, за да направи производството на вермикуларно желязо стабилно и надеждно.
За двигатели с вертикално желязо от прототип до масово производство решаващият фактор е рискът за качеството. За висококачественото вермикулярно желязо стабилната зона е много малка, само в диапазона от 0.008% съдържание на магнезий. Определено количество, като например загуба на 0.001% магнезий, ще доведе до люспест графит, което ще доведе до намаляване на механичните свойства с 25% до 40%. Тази статия описва система за управление на процеса, базирана на методи за термичен анализ. Системата измерва загубата на магнезий и регулира състоянието на разтопеното желязо онлайн, за да предотврати образуването на люспи графит. Този онлайн метод за контрол на измерване и регулиране намалява променливостта в процеса на производство на вермикуларно желязо до най -ниската точка и елиминира фундаментално риска за качеството, причинен от производството на вермикулярно желязо.
Търсенето на високи конски сили, висок въртящ момент, ниски емисии на отработени газове и намален разход на гориво продължава да расте. Това принуждава дизайнерите на дизелови двигатели с висока мощност да увеличат пиковото налягане на запалването, което значително увеличава топлинното натоварване и механичното натоварване на двигателя. Термичното натоварване и механичното натоварване се увеличават едновременно, така че конвенционалните двигатели от чугун и легиран чугун (CrMo), използвани понастоящем, са достигнали или надхвърлили горната граница на тяхното използване. Производителите на двигатели се нуждаят от материали с по -висока якост и по -добра устойчивост на топлина.
Вермикуларното желязо бързо се превърна в изборен материал за хората. Това значително подобрява надеждността на блока на цилиндрите, цилиндровата глава и цилиндровата облицовка от новото поколение двигатели на камиони. За да се постигне най -добрата комбинация от различни свойства (като свойства на леене, механични свойства, топлопроводимост и механични свойства), тези части трябва да бъдат направени със степен на сфероидизация от 0% до 20% (пълзене от 80% до 100% ) Изработен от вермикуларно желязо. Ако процентът на сфероидизация надвишава 20%, това ще предизвика редица неблагоприятни фактори. Например, количеството на свиване е твърде голямо, а части със сложни форми, като глави на цилиндрите, са особено склонни към свиване. Друг пример е намаляването на живота на инструмента поради прекомерното износване по време на обработката. Наблюдава се и значително намаляване на топлопроводимостта, причинявайки термичен стрес и т.н. В другия край на вермуларното желязо появата на люспест графит ще доведе до линеен спад в механичните свойства, което ще направи двигателя неспособен да отговори на новите изисквания. В обобщение, за да се отговори на нуждите на новото поколение двигатели на камиони, степента на сфероидизация на високоякостното вермикулярно желязо трябва да бъде между 0% и 20% (тоест скоростта на пълзене е над 80%, без люспи).
Дали да се използва контрол на производствения процес или не зависи от годишната продукция на продукта, сложността на продукта и допустимия диапазон от промени в металографската структура. Както е показано на фигура 1, сравнително прости части с малък обем, като например форми за слитъци, обикновено могат да бъдат произведени чрез конвенционални методи за леене. Контролът на процеса обикновено не е необходим и не е икономически рентабилен. Когато годишното производство на компоненти се увеличи, като изпускателни тръби, манивела и скоби, трябва да има смисъл да се въведе контрол на процеса. Въпреки че този вид продукт има голяма годишна продукция, годишният тонаж на леене не е висок. Изискванията към металографската структура не са много строги, което позволява процентът на сфероидизация да достигне до 50%. В допълнение, поради малкото количество обработка на такива части, увеличаването на титана, което може да се добави в производството, може да позволи да се разшири контролираният диапазон. За този вид продукти конвенционалните методи на леене и стриктното обучение обикновено са компетентни за производството на вермикулярно желязо. Но от гледна точка на контрола на качеството, контролът на процеса трябва да бъде по -сигурен. По същия начин контролът на процесите също осигурява гаранция за производството на големи блокове за двигатели на корабите и глави на цилиндри. Въпреки че големият размер и ниското количество производство са благоприятни за производството на продукти, икономическите загуби, причинени от продуктите, надвишаващи стандарта, са достатъчни, за да се добави набор от система за контрол на процеса.
Продуктите, които най -много се нуждаят от контрол на процесите, са блокове на цилиндрите на автомобилни двигатели, цилиндрични глави и спирачни дискове с голяма годишна производителност, висока сложност и строги технически изисквания. Годишният обем на производство и годишен тонаж на тези продукти са много високи. Те са сложни по размер, изискват металографска структура и са склонни да произвеждат свиващи се кухини. Тези продукти не трябва да носят никакви рискове за качеството, в противен случай загубата ще бъде много сериозна.
Строгите изисквания за производителността на блока на двигателя, цилиндровата глава и седалката на цилиндъра поставиха основата за производствените спецификации на продукта. За да се постигне най -доброто цялостно представяне на отливката, обработваемостта и механичните свойства, процентът на сфероидизация трябва да бъде в диапазона от 0% до 20% във всички ключови части на компонента. По -важното е, че графитът на люспи трябва да се избягва абсолютно, за да се предотврати повреда на части, причинена от локална слабост. За да се постигне добра механична добавка, свободните карбиди трябва да бъдат намалени до минимум. Следователно титанът никога не трябва да се добавя. И накрая, от гледна точка на производството, леярната се нуждае от стабилен и надежден процес, за да осигури най -ниската норма на бракуване, причинена от металографската структура. Производителите в автомобилната индустрия изискват осигуряване на качеството, а 100% от отливките трябва да отговарят на металографските изисквания. Мащабното и надеждно производство на блокове цилиндри, глави на цилиндри и седалки на цилиндрите изисква точен анализ и онлайн настройка на разтопено желязо, за да се елиминират колебанията в процеса преди изливането.
Вермикуларна стабилност на желязото
Причината, поради която уплътненото желязо не се използва в големи количества за производство на сложни части (като блокове на двигателя), е, че стабилната площ на уплътненото желязо е твърде малка, за да се гарантира, че няма риск при производството. Най -общо казано, тази стабилна зона обхваща само площта от 0.008% магнезий, както е показано на фигура 2. Размерът и позицията на платформата в стабилната зона варират в зависимост от продукта. Всъщност наличният магнезиев диапазон е по -малък от този. Тъй като на всеки 5 минути, активният магнезий ще гори 0.001%. Първоначалната точка на изливане на разтопеното желязо трябва да бъде достатъчно далеч от острата точка на завъртане на уплътненото желязо към сивото желязо, за да се гарантира, че в крайната отлита част не се появява люспест графит. Когато към разтопеното желязо се добави магнезий, графитът ще се появи след около 15 минути.
Изходната точка не трябва да е твърде близо до дясната страна на стабилната платформа (високо съдържание на магнезий), в противен случай това ще доведе до образуване на голямо количество сфероиден графит в по -тънката част и бързо охлаждащата се част.
В допълнение към малката налична площ на платформата, зоната на платформата винаги се движи. Ако съдържанието на активен кислород и сяра е високо, те ще консумират повече активен магнезий и цялата платформа ще се премести надясно (високо съдържание на магнезий). И обратно, ако съдържанието на активен кислород и сяра е ниско, платформата ще се премести наляво (ниско съдържание на магнезий). Промените в състава на суровините, чистотата, степента на окисление и влажност и др. Правят хората невъзможни да контролират ядрено желязо с фиксиран диапазон от химичен състав.
Въпреки че при превръщането от червеното желязо в сиво желязо е необходимо само да се намали активният магнезий с 0.001%, изгарянето на магнезия не кара цялата част да се превърне в люспест графит. Когато активният магнезий не е достатъчен, графитът първо образува люспи и се разширява навън при втвърдяването си, а магнезият провисва и се концентрира в предния край на границата между твърдо и течно вещество. Ако първоначалното количество активен магнезий е подходящо, вермикуларен графит ще се образува на границата на евтектиката, както е показано на фигура 3. Графитът на люспи се появява първо като разпръснати графитни петна на люспи. За разлика от всички обикновени графити на люспи, тези изолирани люспирани графитни петна са трудни за откриване с ултразвук. Вероятността те да бъдат сканирани чрез ултразвук не е голяма.
Чувствителността на магнезия към вермикуларно желязо може да бъде показана на Фигура 4: В тон горещ метален черпак, просто добавете 10 грама магнезий, графитните петна на люспи, разпръснати в тестовата проба Φ25, могат да бъдат напълно трансформирани в вермикуларен графит. Якостта на опън на изпитвателната пръчка с графитни петна на люспи е само 300 МРа, докато якостта на опън на същата изпитвателна лента с пълно пълзене достига 450 МРа.
Инокулантът също е много чувствителен към стабилната платформа от вермикулярно желязо, както е показано на фигура 5: добавянето на 80 грама инокулант към един тон разтопено желязо ще увеличи степента на сфероидизация в тестовата лента Φ25 от 3% на 21%. Количеството на инокулацията е високо, а кристалното ядро е много, което благоприятства образуването на сферичен графит. Това повдига вермикулярната желязна платформа в посока на висока скорост на сфероидизация. Ниският процент на инокулация кара платформата да се движи надолу. Многобройни фактори, като температура на прегряване на разтопено желязо, време на задържане, химичен състав на суровините, тип инокулант и количество на инокулацията, ще повлияят на позицията на вермикулярната желязна платформа.
Най -основното изискване на всяка технология за управление на процеса е точното измерване и анализ на състоянието на разтопеното желязо. За вермуларно желязо надеждният производствен контрол изисква едновременно измерване на критичната точка на активния магнезий от прехода на пълзене-пепел, степента на последващо изгаряне на магнезий и степента на инокулация.
Пробата за термичен анализ от 200 грама се получава чрез поставяне на сондата Xinte в разтопеното желязо след сфероидизация и инокулация. По време на трисекундния процес на вмъкване стената на сондата и разтопеното желязо достигат състояние на термично равновесие. За разлика от конвенционалната чаша за проба за термичен анализ, този тънкостенен пробоотборник не само гарантира същия обем проба всеки път, но и избягва окисляването в разтопеното желязо, което се излива в чашата за проба. Измерването на прегряване е по -точно, тъй като в конвенционалния термичен анализ няма такова явление като явлението насилствена кондензация.
Както е показано на фигура 6а, сондата Xinte е направена от пресована опъната стоманена ламарина. По същество това е сферичен контейнер. Тънката стоманена стена, съдържаща разтопеното желязо, има изолационен слой, наподобяващ вакуумна колба. Дебелината на изолационния слой е симетрично удебелена според посоката на височината, за да се осигури равномерно разсейване на топлината и охлаждане към околната среда, а желязната вода zz в него е близо до втвърдяването на сферично тяло. В защитната тръба на сондата има две термодвойки тип N. Термодвойката може да се изтегля след всяко измерване и да се използва многократно повече от 100 пъти. Едната от двете термодвойки се намира в долната част на контейнера, а другата се намира в термичния център на контейнера. Тъй като контейнерът е сферичен и свободно окачен (това е различно от конвенционалната чаша за проби за термичен анализ, лежаща на топлопоглъщаща скоба), разтопеното желязо генерира равномерен топлинен поток в контейнера, както е показано на фигура 6б. Този топлинен поток кара разтопеното желязо да се обменя непрекъснато в контейнера, образувайки поточна преграда в дъното на сондата.
За да се имитира естествената загуба на разтопено желязо по време на изливането, върху стената на сондата има покритие, което реагира с активен магнезий. Разтопеното желязо тече по покритата стена, задвижвана от топлинния поток. След реакцията съдържанието на магнезий в разтопеното желязо намалява и се натрупва в отделението на дъното на контейнера. Директно казано: Термодвойката в центъра на сондата измерва нереагиралото разтопено желязо, което е първоначалното състояние на изливане; термодвойката в долната част измерва състоянието след края на изливането. Формулировката на реактивното покритие е много специфична. Трябва да се гарантира точно, че разтопеното желязо, натрупано в отделението, е с 0.003% по -малко активно от централното разтопено желязо. Следователно, ако първоначалното съдържание на магнезий е твърде близо до точката на завъртане на пълзящата пепел, разтопеното желязо в отделението ще генерира сиво желязо, което ще бъде измерено чрез термодвойката в тази област. По този начин в началото на леенето работилницата може да добави още магнезий, за да компенсира неизбежната загуба на изгаряне на магнезий.
Ако термодвойката в долната част показва вертикална желязна крива, това показва, че първоначалното съдържание на магнезий е достатъчно високо, че няма да има люспин графит след края на отливането.
Фигура 7 е диаграма на ерозия на напречното сечение на сондата Xinte след измерване на пробата. На фигурата можете ясно да видите зоната на преградата, основната зона за проба и защитната тръба на термодвойката. Тъй като активният магнезий се намалява с 0.003%, в зоната на разделяне се образуват D-образна графитна и феритна матрица. Размерът на графитната площ на люспите в долната част отразява директно първоначалното съдържание на магнезий в основната зона на пробата. Размерът на тази зона може да се изчисли от топлината, отделена на дъното. Коефициентът на регресия на дисперсията между отделянето на топлина и размера на преградата надвишава 0.9, което доказва, че връзката между двете е много близка. Освободената топлина се получава чрез интегриране на времето на кривата на охлаждане. Този метод за измерване на състоянието на разтопеното желязо в момента и в края на изливането едновременно гарантира точността на съдържанието на магнезий преди изливането.
Тъй като червеното желязо е много чувствително към сфероидизиращи агенти и инокуланти, леярните не могат да използват прекомерните методи за обработка, използвани при производството на сиво желязо и ковък чугун. Както е показано на фигура 8, поради своята чувствителност, вермикулярното желязо е стабилно само в квадратен прозорец, а не само в областта на магнезиевата платформа. Надеждният процес на производство на червено желязо трябва да контролира сфероидизацията и инокулацията от началото до края, за да се гарантира, че металографската структура отговаря на целта.
Колкото и усилия да се полагат, колкото и строго да се управлява, колебанията на разтопеното желязо винаги са неизбежни. Да не говорим за това колко точно хората знаят за обработката на разтопено желязо, едноетапните методи на лечение, като например метода на сандвича, не могат да гарантират, че всяко третиране ще попадне в тесния вертикален железен прозорец. Многобройни производствени променливи, като съотношение на смесване, температура на пещта, време на задържане, степен на предварително загряване на черпак от разтопено желязо, скорост на потупване, позиция на потупване на разтопено желязо (вътрешно или външно измерване), тегло на разтопено желязо, състояние на торбата от сплав, сфероидизиращ агент действителното съдържание на магнезий в (PeSiMg), подреждането на сплавите на всеки слой в метода на сандвича и покритието на стърготини от скрап и т.н., ще повлияят на усвояването на магнезия. В допълнение към тези фактори, съдържанието на активен кислород и активна сяра също ще промени размера и позицията на прозореца с червеникаво желязо. Промените във времето на престой на разтопеното желязо в черпака, времето за транспортиране и времето за изливане ще променят наличното време на горене.
Най -непредсказуемите фактори на колебания обаче са грешките на оператора или различията между различните оператори поради различни работни навици.
При масово масово производство единственият безопасен начин е да се измерват характеристиките на втвърдяване на разтопеното желязо след третиране. По този начин различни фактори, влияещи върху размера, положението и абсорбцията на сплави на прозореца от вермикулярно желязо, са изчерпателно измерени, анализирани и отчетени. След това може да се добави подходящото количество магнезий и инокулант. Всеки черпак разтопено желязо се излива, след като е надграден до идеално състояние. Този двустепенен метод за контрол на процеса на измерване и регулиране минимизира променливостта на производството и напълно елиминира риска от лющене на графит при отливането.
Контрол на процеса на производство на вертикално желязо с черпак от горещи метали
Както е показано на Фигура 9, контролът на процеса започва с термичния анализ на разтопеното желязо след първоначалната сфероидизация и инокулационна обработка. Според резултата от анализа машината за подаване на тел автоматично показва дължината на телта, която трябва да се добави с магнезий и инокулант, и чака оператора да я стартира. Когато захранващата линия е завършена, черпакът веднага се изпраща към линията за леене. Целият процес на измерване и настройка отнема около три минути. През този период работилницата може да извършва конвенционални предварителни обработки, например отстраняване на шлака. Това гарантира непрекъснатостта на леярската линия.
От оперативна гледна точка, суровото разтопено желязо не съдържа магнезий и инкубационният му капацитет също е много ограничен. След сфероидизация и инокулиране, магнезият и инокулантите първо изяждат активния кислород и сярата в разтопеното желязо и след това „прескачат“ разтопеното желязо до определена позиция на дъската. В примера на фигура 10, магнезиевият индекс и инсулационният индекс на разтопено желязо са съответно 65 и 45. Тъй като основните параметри на промяна на производството на сянка са показани в разтопеното желязо след измерване и обработка, резултатите от термичния анализ директно отразяват текущото състояние на разтопеното желязо. Остава само да добавите подходящо количество магнезий и инокулант, за да издигнете разтопеното желязо от текущото му положение до необходимата начална точка. В примера на фигура 10 първо се добавят седем единици магнезиеви кабели, а след това се добавят 23 единици кабели за инокулация. Съответната връзка между единицата за индекс и дължината на кабела се калибрира според продукта и сервиза и се компилира в програмата. Въз основа на миналия опит с почти 100,000 5 чугунени отливки, средното количество добавен магнезиев кабел е 12 метра на тон. Той съдържа 50 грама магнезий на метър и изчислено при степен на абсорбция 30%, количеството добавен магнезий на тон разтопено желязо е само XNUMX грама. Тъй като добавената сума е много малка и основните промени вече са настъпили при първоначалното третиране, корекцията е много ефективна и надеждна. След регулиране няма нужда да правите термичен анализ.
При първоначалното третиране състоянието след третирането трябва да е по -ниско от първоначалното положение за изливане, така че дори ако всички фактори, които са полезни за усвояването на магнезия и инокуланта, достигнат оптималната стойност, разтопеното желязо ще достигне само първоначалното състояние на изливане . С изключение на прекомерното третиране, разтопеното желязо след обработката не е в състояние на сиво желязо и бяло желязо. За да се направи процесът на леене по -ефективен, магнезиевият индекс и индексът на инокулация на всеки черпак разтопено желязо се показват в блоковата схема на процеса. Според променящата се тенденция на блоковата диаграма, операторът може да регулира количеството разтопено желязо, добавено към следващия черпак. Стойността на еквивалента на въглерода също се показва на екрана. Тези данни са редактирани и съхранявани в производствения дневник, така че да могат да бъдат проследени и изчерпателни, а също така отговарят на изискванията за осигуряване на качеството.
Въпреки че термичният анализ и последващите корекции могат да осигурят производството на вермикуларно желязо, се препоръчва да се вземат проби от чашата за изливане на крайната отливка за анализ. В сравнение с конвенционалната проверка на качеството, този резултат от термичен анализ може да осигури онлайн анализ и да класифицира отливките, ако е необходимо. Симулацията на загуба на магнезий в сондата прави тази "неразрушителна" техника на инспекция по-ефективна от металографските и ултразвуковите методи. Тъй като този метод измерва по-голям размер на пробата, той също така открива как разтопеното желязо ще се втвърди в следващите 10-15 минути.
Да обобщим
Изборът на система за контрол на процеса зависи от продукта и процеса на леене. При леене на сложни продукти като капак и цилиндър от вертикално желязо, системата трябва едновременно да контролира съдържанието на магнезий и инокулант, така че да е в много тесен прозорец от началото до края на изливането. Степента на сфероидизация трябва да бъде между 0% и 20% (пълзяща честота 80% до 100%), за да се гарантира най -добрата отливка, механична добавка и други цялостни характеристики и най -добрата функция за използване. Графитните петна на люспи трябва да бъдат напълно отстранени, за да се предотвратят локални дефекти и слабости.
Отправната точка на всяка система за контрол на процеса е точно и ефективно измерване на състоянието на разтопеното желязо. Надеждното мащабно производство на червено желязо трябва да има осъществими методи за контрол, за да се елиминират промените в процеса и грешките при работа на човека. Най -ефективният начин за премахване на промените в процеса е да се проведе термичен анализ върху разтопено желязо след сфероидизация и инокулация. Според резултатите от термичния анализ, преди изливане се добавят точно количество магнезий и инокулант. Този метод за онлайн измерване и регулиране гарантира стабилността на производствената линия за леене и елиминира различни рискове, породени от мащабното производство на вертикално желязо.
Моля, запазете източника и адреса на тази статия за повторно отпечатване: Процесният контрол на производството на вермикулярно желязо
Мингхе Компания за леене на умира са посветени на производството и осигуряват качествени и висококачествени части за леене (обхватът на части за леене на метали включва главно Тънкостенно леене под налягане,Топъл камер Die Casting,Студено камерно леене), Кръгло обслужване (услуга за леене под налягане,Cnc обработка,Изработка на плесени, Повърхностна обработка). Всички персонализирани алуминиеви отливки, леене с магнезий или Zamak / цинк и други отливки са добре дошли да се свържете с нас.
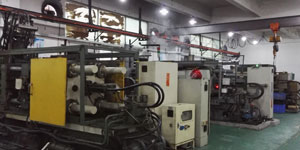
Под контрола на ISO9001 и TS 16949, всички процеси се извършват чрез стотици усъвършенствани машини за леене под налягане, 5-осни машини и други съоръжения, вариращи от бластери до Ultra Sonic перални машини. Minghe не само разполага с модерно оборудване, но и разполага с професионални екип от опитни инженери, оператори и инспектори, за да реализират дизайна на клиента.
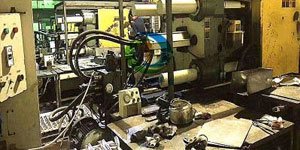
Договорен производител на отливки. Възможностите включват части за леене от алуминий със студена камера от 0.15 lbs. до 6 lbs., настройка за бърза смяна и обработка. Услугите с добавена стойност включват полиране, вибриране, отстраняване на обезкосмяването, струйно взривяване, боядисване, покритие, покритие, монтаж и обработка на инструменти. Материалите, с които се работи, включват сплави като 360, 380, 383 и 413.
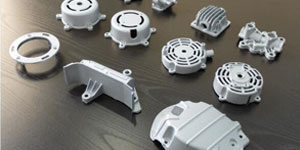
Помощ при проектиране на леене на цинк при съпътстващи инженерни услуги Персонализиран производител на прецизни отливки от цинкова матрица. Могат да се произвеждат миниатюрни отливки, отливки под високо налягане, отливки с многоплъзгащи се форми, конвенционални отливки за форми, единични матрици и независими отливки и отливки с кухина Отливките могат да се произвеждат с дължина и ширина до 24 инча в толеранс +/- 0.0005 инча.
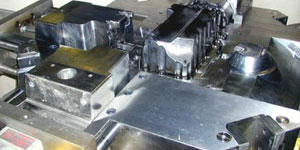
ISO 9001: 2015 сертифициран производител на магнезиево леене под налягане, Възможностите включват магнезиево леене под високо налягане до 200 тона гореща камера и 3000 тона студена камера, дизайн на инструментите, полиране, формоване, обработка, боядисване на прах и течности, пълен QA с CMM възможности , монтаж, опаковане и доставка.
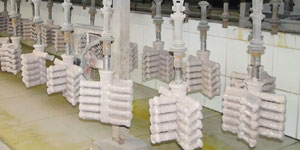
Сертифициран по ITAF16949 Включва допълнителна услуга за кастинг инвестиционно леене,пясъчно леене,Гравитационен кастинг, Изливане на пяна леене,Центробежно леене,Вакуумно леене,Постоянно леене на мухъл, .Възможностите включват EDI, инженерна помощ, солидно моделиране и вторична обработка.
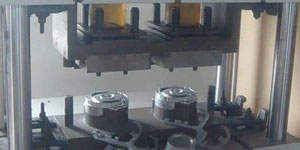
Кастинг индустрии Казуси за части за автомобили: Мотори, Самолети, Музикални инструменти, Водни плавателни съдове, Оптични устройства, Сензори, Модели, Електронни устройства, Кутии, Часовници, Машини, Двигатели, Мебели, Бижута, Конзоли, Телеком, Осветление, Медицински изделия, Фотографски устройства, Роботи, скулптури, озвучителна техника, спортна екипировка, инструментална екипировка, играчки и др.
Какво можем да ви помогнем да направите по-нататък?
∇ Отидете на началната страница за Китай за леене под налягане
→Части за леене-Разберете какво сме направили.
→ Съпоставени съвети за Услуги за леене под налягане
By Производител на леене под налягане Minghe | Категории: Полезни статии |Материал Tags: Алуминиево леене, Цинково леене, Магнезиево леене, Титаново леене, Леене от неръждаема стомана, Месинг леене,Бронзово леене,Кастинг на видео,История на компанията,Алуминиево леене под налягане | Коментарите са изключени