Захранваща тел Метод Процес на обработка с пластично желязо
Чрез реално производство, методът на щанцоване и методът на подаване се използват за производство на пластично желязо и се анализират характеристиките на двата процеса. Чрез сравнението цялостното изпълнение на отливките, произведени чрез метода на подаване, е по -стабилно от това на метода на щанцоване; и процесът на хранене е сфероидизиран. Да споделя някои от преживяванията в него.
1. Преглед
Както всички знаем, оста е важна носеща част от превозното средство и е пряко свързана с безопасността на превозното средство. Корпусът на оста е един от ключовите компоненти на оста. Производителността на материала на корпуса на оста директно определя товароносимостта на превозното средство. Понастоящем корпусите на осите в индустрията на тежкотоварни камиони обикновено се разделят на две категории: щамповани и заварени корпуси на оси и корпуси от чугунени оси, а корпусите от чугунени оси могат да бъдат разделени на корпуси от оси от чугун и корпуси от оси от чугун.
Корпусът на отлитата ос винаги е заемал основното място на корпуса на оста на тежкотоварен камион поради голямото си носещо тегло и ниските производствени разходи. Поради тежката работна среда на корпуса на оста и продължителната работа при динамично натоварване, това изисква високи изисквания към свойствата на материала на корпуса на оста. Докато гарантира здравината, тя също така трябва да получи по -висока пластичност и здравина, за да се адаптира към корпуса на оста. Характеристики на работа.
Знаем, че за нодуларен чугун процесът на сфероидизиране е ключова връзка в производството на нодуларен чугун и качеството на сфероидизиращата обработка влияе пряко върху качеството на нодуларния чугун. В началото процесът на сфероидизиране, който използвахме, беше процесът на сфероидизиране по метода на бърза атака. Въпреки че този метод е прост и лесен за работа, той има много недостатъци, като например: нисък добив на сплави; голям дим и лоша работна среда; реакция Количеството на получената шлака по това време е голямо; лечебният ефект лесно се влияе от външни фактори, което води до колебания в качеството на отливките и често до неквалифицирана сфероидизация. Тези колебания в качеството ще повлияят на работата на корпуса на оста и дори ще повлияят на безопасността на автомобила.
Процесът на сфероидизиращо третиране на метода на подаване на тел е приложен за производството на чугун. Започва през 1980 -те години в чужбина. Въпреки че местното производство на нодуларен чугун започна да прилага тази технология късно, технологията е популяризирана и използвана бързо в страната и е полезна за подобряване на производството на нодуларен графит. Ефектът на стабилност на качеството на чугуна е очевиден.
2. Процес на сфероидизиране на захранващата тел
Основният принцип на процеса на подаване на сфероидизиращи нишки е да се увие определен състав от прахообразен сфероидизиращ агент и инокулант през стоманената обвивка и да се изпрати в пакета за сфероидизираща обработка с определена скорост през оборудването, така че сфероидизирането в долната част на пакетът ще се взриви. За да се постигне целта на инокулационното лечение със сфероидизация.
Понастоящем процесът на сфероидизиране на захранване с тел, който приемаме, е: нагласете химическия състав към изискванията на процеса, загрейте до 1510-1520 ℃ и оставете да стои неподвижно, температурата на потупване е 1480 ~ 1500 ℃, желязото е 2t и температурата на сфероидизиращата обработка е 1420 ~ 1450 ℃. Температурата на изливане е 1370 ~ 1380 ℃. Степента на инокулация с потока е 0.1%.
Дължината на сфероидизиращата линия е 39-46 м, коригирана според съдържанието на сяра в оригиналното разтопено желязо. Колкото по -високо е съдържанието на сяра, толкова по -дълго трябва да се добави сфероидизиращата линия и обратно. Дължината на инокулационната линия е 32 метра.
3. Сфероидизиращият процес на подаване на тел подобрява качеството на отливките
След повече от година на производство, качеството на нашите корпуси на осите е значително подобрено в сравнение с преди. Особено стабилността на състава, металографията и механичните свойства са значително подобрени.
Сравнение на металографската структура Изберете същата позиция на отливката за полиране и наблюдавайте металографската структура. Направената металографска снимка е показана на фигура 2. В сравнение с метода на щанцоване, графитните топки от отливката, произведени по метода на подаване, са по -тънки и закръглеността е по -добра.
4. Предимства на процеса на сфероидизация на захранващите нишки
Според нашето реално сравнение на производството, процесът на сфероидизиране на подаване на нишки има много предимства пред процеса на сфероидизиране на метода на щанцоване.
- Подобряване на производствената среда на място. Когато сфероидизиращият агент реагира с разтопеното желязо, се генерира голямо количество дим и силна светлина, което влошава работната среда на място; когато методът за подаване на тел се използва за сфероидизация, преработвателната станция Има капак за покриване на торбата за сфероидизация, а капакът е свързан към системата за отстраняване на прах на преработвателната станция, така че димът се обработва от системата за прахоулавяне вместо да бъдат пуснати директно в работилницата.
- Количеството добавена сплав се намалява и производствените разходи се намаляват. След изчисление, обработката на 1т метод на подаване на разтопено желязо може да спести около 78 юана в разходите за суровини, отколкото импулсния метод. Според годишния производствен капацитет от 10,000 780,000 тона корпус от ос от ковано желязо на нашата фабрика, годишната икономия е Цената е XNUMX XNUMX юана и ползите са значителни.
- Реализирайте автоматизация на работните места и намалете трудоемкостта на работниците. Когато се извършва процесът на сфероидизация, предварителните подготовки на работниците са тромави, включително претеглянето на сфероидизиращия агент и инокуланта, добавянето на сфероидизиращия агент и инокуланта в торбата, както и набиването и покриването; добавянето на количество от сфероидизиращите и инокулиращите линии на метода за подаване на нишки се добавя автоматично през шкафа за управление, което намалява много работа.
- Качеството на сфероидизацията е стабилно и ефектът на сфероидизацията е по -добър. Според статистиката, след използването на процеса на сфероидизация с подаване на нишки през 2013 г., процентът на преминаване на сфероидизацията е над 99.5 %, докато процентът на преминаване на процеса на сфероидизация е само 95. %.
5. Как правилно да изберем параметрите на процеса на сфероидизация на подаващата нишка
В действителното производство, за да изберете правилно параметрите на процеса на подаване на тел, е необходим определен брой тестове за проверка. Претърпели сме много промени в процеса от началото на организацията на теста до официалното масово производство. Следното ще сподели нашия опит с колегите.
За да изберете правилно параметрите на процеса на сфероидизация на захранващата нишка, трябва да обърнете внимание на следните аспекти:
- (1) Изборът на жила с проводник Някои чуждестранни опити не препоръчват използването на проводник с високо съдържание на Mg. Съдържанието на Mg е твърде високо, реакцията на сфероидизация е интензивна, Mg изгаря много и количеството шлака е голямо. Обикновено се препоръчва да се избере съдържание на Mg от около 30%и да се използва нишка за инокулация, съдържаща Ba, което може ефективно да предотврати спада на инокулацията. Основните параметри на жилата, използвана от нашата компания, са: дебелината на външната стоманена обвивка е 0.4 мм, а диаметърът на жилата на жилата е 13 мм. Преди употреба проверете дали външният проводник трябва да е кръгъл и без пукнатини, изтичане на прах и др. При реално производство е необходимо да се регулира според температурата на обработка и височината на разтопеното желязо. Като цяло, колкото по -висока е температурата на обработка, толкова по -висока е височината на разтопеното желязо и по -бързата скорост на подаване на телта. В допълнение. Някои материали също така въведоха удобен и възможен метод за измерване на оптималната скорост на подаване на тел: първо измерете височината на разтопеното желязо в торбата за обработка и след това ръчно подайте машината за тел, така че жилата на сърцевината само да докосне повърхността на течността, след това изчистете брояча, Ръчната машина за подаване на тел извършва подаване на тел. Когато чуете звука за реакция "бум", незабавно проверете дължината на подаване. Ако тази дължина е основно равна на височината на разтопеното желязо, скоростта трябва да е подходяща. След проверка избрахме скорост на подаване от 30 м/мин.
- Избор на количество подаване на нишка Подходящото количество подаване на нишка е да се подаде най -малко сърцевината на нишката при предпоставката за осигуряване на ефекта на сфероидизация. Количеството подаване на тел трябва да се определи според обема на обработката на разтопеното желязо, температурата на обработка и съдържанието на сяра в разтопеното желязо. Съгласно нашите първоначални изисквания за съдържание на сяра в разтопено желязо и производствен процес, комбинирани с експериментална проверка, при условие, че се гарантира остатъчното съдържание на магнезий, дължината на сфероидизиращата линия е 39-46 m, а дължината на инокулационната линия е 32 m.
- Избор на температура на обработка Температурата на обработка трябва да бъде намалена колкото е възможно при предпоставката за осигуряване на температурата на изливане. Колкото по -ниска е температурата на обработка, толкова по -висока е скоростта на абсорбция на магнезий и по -малка консумация на сърцевина от сърцевина. Според реалните производствени тестове, времето от началото на сфероидизиращото третиране до началото на изливането е 4 до 5 минути, през което спадането на температурата е 40 до 50 ° C, а времето на сфероидизираща реакция е 80 до 90 секунди. Тъй като процесът на сфероидизиране трябва да се обърне, ние задаваме температурата на обработка на 1410 ~ 1450 ℃, горната граница се взема, когато стайната температура е по -ниска от 5 ℃, а долната граница, когато стайната температура е по -висока от 25 ℃.
- Избор на остатъчно съдържание на магнезий в разтопено желязо след третиране. Остатъчното съдържание на магнезий трябва да се отдели за определено количество магнезий според характеристиките на самата отливка. Първоначално ние контролирахме съдържанието на остатъчен магнезий до 0.03% до 0.06%, но след реална проверка на производството е по -подходящо да се контролира остатъчното съдържание на магнезий до 0.05% до 0.06%, защото установихме, че когато остатъчният магнезий е по -малък от 0.04%, нейният графит Закръглеността на топката е малко по -лоша. Когато той е по -висок от 0.07%, е склонен да се появи циментит и тенденцията на свиване на разтопеното желязо става по -голяма.
- Решаване на проблема със засядане на проводници по време на употреба Феноменът заседнал проводник ще възникне по време на транспортирането на жилата със сърцевина, което ще доведе до бракуване на цялата опаковка разтопено желязо. За тази цел сме предприели следните мерки: една е да инсталираме стоманен пръстен над макарата със сърцевина, както е показано на фигура 5, което може да намали огъването на жилата на сърцевината и да я накара да влезе плавно в направляващия механизъм; втората е свързването на двете намотки При заваряване, след заваряване, излъскайте по -големите неравности, за да предотвратите задръстване на проводника по време на транспортиращия процес; на трето място, избягвайте завоите с диаметър по -малък от 1 м в тръбопровода за транспортиране или трасето на жилата със сърцевина, за да предотвратите транспортирането на сърцевината от тел.
6 Заключение
- Процесът на сфероидизиране на метода на захранваща тел има ниско количество добавяне на сплави, висока степен на абсорбция на Mg и може ефективно да намали дима и силното светлинно замърсяване в цеха, създавайки добри икономически и екологични ползи за леярските предприятия.
- Процесът на сфероидизация на метода за подаване на нишки може ефективно да намали степента на неуспех на сфероидизацията, да подобри качеството на нодуларен чугун, да подобри неговите цялостни механични свойства и да повиши пазарната конкурентоспособност на предприятието.
- Всяка леярна трябва да избере подходящите технологични параметри за сфероидизация на тел според собствените си производствени условия и изискванията на производствения процес, съчетани с производствения опит на колегите.
Процесът на сфероидизиране на захранващата линия може значително да подобри стабилността на качеството на нодуларен чугун, да намали производствените разходи, да подобри производствената среда и да намали трудоемкостта на работниците. Това е скорошната тенденция на развитие на сфероидизиращия процес.
Моля, запазете източника и адреса на тази статия за повторно отпечатване: Feeding Wire Method Процес на обработка с ковък чугун
Мингхе Компания за леене на умира са посветени на производството и осигуряват качествени и висококачествени части за леене (обхватът на части за леене на метали включва главно Тънкостенно леене под налягане,Топъл камер Die Casting,Студено камерно леене), Кръгло обслужване (услуга за леене под налягане,Cnc обработка,Изработка на плесени, Повърхностна обработка). Всички персонализирани алуминиеви отливки, леене с магнезий или Zamak / цинк и други отливки са добре дошли да се свържете с нас.
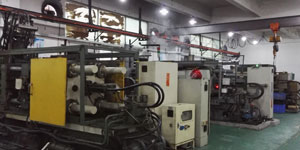
Под контрола на ISO9001 и TS 16949, всички процеси се извършват чрез стотици усъвършенствани машини за леене под налягане, 5-осни машини и други съоръжения, вариращи от бластери до Ultra Sonic перални машини. Minghe не само разполага с модерно оборудване, но и разполага с професионални екип от опитни инженери, оператори и инспектори, за да реализират дизайна на клиента.
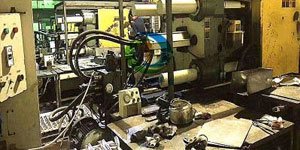
Договорен производител на отливки. Възможностите включват части за леене от алуминий със студена камера от 0.15 lbs. до 6 lbs., настройка за бърза смяна и обработка. Услугите с добавена стойност включват полиране, вибриране, отстраняване на обезкосмяването, струйно взривяване, боядисване, покритие, покритие, монтаж и обработка на инструменти. Материалите, с които се работи, включват сплави като 360, 380, 383 и 413.
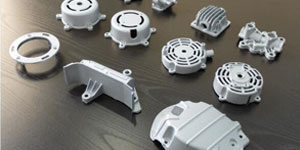
Помощ при проектиране на леене на цинк при съпътстващи инженерни услуги Персонализиран производител на прецизни отливки от цинкова матрица. Могат да се произвеждат миниатюрни отливки, отливки под високо налягане, отливки с многоплъзгащи се форми, конвенционални отливки за форми, единични матрици и независими отливки и отливки с кухина Отливките могат да се произвеждат с дължина и ширина до 24 инча в толеранс +/- 0.0005 инча.
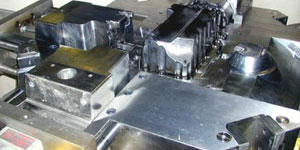
ISO 9001: 2015 сертифициран производител на магнезиево леене под налягане, Възможностите включват магнезиево леене под високо налягане до 200 тона гореща камера и 3000 тона студена камера, дизайн на инструментите, полиране, формоване, обработка, боядисване на прах и течности, пълен QA с CMM възможности , монтаж, опаковане и доставка.
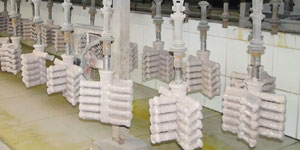
Сертифициран по ITAF16949 Включва допълнителна услуга за кастинг инвестиционно леене,пясъчно леене,Гравитационен кастинг, Изливане на пяна леене,Центробежно леене,Вакуумно леене,Постоянно леене на мухъл, .Възможностите включват EDI, инженерна помощ, солидно моделиране и вторична обработка.
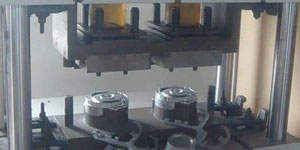
Кастинг индустрии Казуси за части за автомобили: Мотори, Самолети, Музикални инструменти, Водни плавателни съдове, Оптични устройства, Сензори, Модели, Електронни устройства, Кутии, Часовници, Машини, Двигатели, Мебели, Бижута, Конзоли, Телеком, Осветление, Медицински изделия, Фотографски устройства, Роботи, скулптури, озвучителна техника, спортна екипировка, инструментална екипировка, играчки и др.
Какво можем да ви помогнем да направите по-нататък?
∇ Отидете на началната страница за Китай за леене под налягане
→Части за леене-Разберете какво сме направили.
→ Съпоставени съвети за Услуги за леене под налягане
By Производител на леене под налягане Minghe | Категории: Полезни статии |Материал Tags: Алуминиево леене, Цинково леене, Магнезиево леене, Титаново леене, Леене от неръждаема стомана, Месинг леене,Бронзово леене,Кастинг на видео,История на компанията,Алуминиево леене под налягане | Коментарите са изключени