Събиране на често срещани дефекти и превантивни мерки при обезгаряването и закаляването
Нагряване и закаляване всъщност е композитен процес, а именно нагряване + закаляване. Често сме свикнали да говорим за двете заедно, тъй като двата процеса, които са завършени на едно и също оборудване, са най-често срещани в производството (но има и процеси на въздушно охлаждане, процеси на бавно охлаждане и след това процеси на повторно нагряване и охлаждане и вторични Процес) Тогава някои от нежеланите явления, които се срещат в производството, са проблеми с карбуризирането, някои са проблемите с охлаждането, а някои са резултат от комбинираните ефекти на карбонизирането и закаляването.
Знаем, че всички процеси на топлинна обработка са неделими от три основни проблема: отопление, запазване на топлината и охлаждане. В подробности, включително температура на нагряване, скорост на нагряване, време на задържане, скорост на охлаждане и, разбира се, проблеми с атмосферата. Така че след като нещо се обърка, ние ще анализираме причината от тези аспекти.
За карборизиране и закаляване често тестваме тези показатели: външен вид на повърхността на продукта, твърдост на повърхността, твърдост на сърцевината, дълбочина на карбуризиран слой, (ефективна дълбочина на втвърдения слой, дълбочина на втвърдения слой) металографска структура и деформация. Нека споделим моите виждания съответно за тези показатели.
1. Проблем с външния вид
1. Оксидна скала: Това се дължи главно на изтичане на оборудване, нечист газ-носител или водно съдържание. Трябва да намерите причината от оборудването и суровините.
2. Другият най-обезпокоителен проблем е проблемът с петна, което също е ново и предизвикателно изискване за термична обработка в съвременността. Причините са сложни и много дълбоки.
две. Неквалифицирана твърдост
1. Висока твърдост (не се обсъжда)
2. Ниска твърдост: Има две ситуации, едната е неквалифицирано карборизиране. Причината може да е, че карборизираният слой е твърде плитък, за да отговори на изискванията на чертежите ((карборизираният слой не е инфилтриран) или избраният мащаб на откриване надвишава съществуващия допустим диапазон на карборизиран слой, което ще разруши карбуризирания слой.
Решение: Напълнете просмукващия филтър и следвайте правилото за проверка. JBT 6050-2006 "Общи принципи за проверка на твърдостта на термичната обработка на стоманени детайли" Дълбочината на цементирания слой всъщност е функция от температурата, времето и въглеродния потенциал. От горните фактори можем да разгледаме начини за увеличаване на температурата на нагряване, удължаване на времето на задържане и увеличаване на потенциала за карборизиране. (Разбира се, настройката на всеки параметър трябва да се комбинира изцяло с изискванията на вашето собствено оборудване и продукти) Може да се дължи и на съществуването на неконни организации на повърхността. Друга ситуация се получава, когато твърдостта е ниска, тоест карборизирането е квалифицирано, но закаляването е неквалифицирано. Най-общо казано, той не е загасен. Тази ситуация е най-сложната, както се казва: термичната обработка разчита на отопление за три четвърти и охлаждане за седем четвърти. Той също така отразява позицията, която процесът на охлаждане заема в процеса на топлинна обработка.
Следва сравнителен тест, който аз проектирах. Можете да обсъдите ефекта на охлаждането върху твърдостта.
Вземете 3 групи тестови пръти с различни материали, но еднакви спецификации и размери, чийто размер е Φ20mmX100mm. (Ние наричаме No 20 стоманена тестова лента № 1, 20Cr тестова лента № 2 и 20CrMnTi тестова лента № 3) Тестовите пръти се карборизират в една и съща топлина, използвайки същия процес. Ако приемем, че дълбочината на въглеродения слой на трите тестови пръта е 0.6-0.7 mm (ps: предположението е установено само в идеално състояние).
Моля, вземете предвид следните условия:
а. Завършете закаляването при същите условия
б. Охлаждащата среда е бавно масло, бързо масло, бистра вода, солена вода
° С. В същата среда, без да се разбърква и интензивно се разбърква и охлажда, трите тестови ленти се вземат в две групи за тестване.
След завършване на карбонизирането А групата се охлажда при 800 градуса, а групата В се охлажда при 860 градуса. Какъв е редът на тяхната твърдост от висока към ниска? Как да поръчам втвърдения слой (с 550HV1.0 като граница) от дълбок до плитък? Вземете две тестови пръти от един и същ материал и сравнете и тествайте, коя група може да получи по-висока твърдост на закаляване и ефективна дълбочина на закаления слой?
Може ли да се заключи от горните резултати от изпитването, че дълбочината на въглеродизирания слой не е равна на дълбочината на ефективния втвърден слой и действителната дълбочина на втвърдения слой се влияе от втвърдяването на материала, температурата на охлаждане и охлаждането ставка. Характеристиките на охлаждане и интензивността на охлаждане на охлаждащата среда също влияят на охлаждащия ефект. По-горе са вижданията на хората, ако има някаква непълнота, можете да добавите. Разбира се, ефектът на размера на частите също влияе върху ефекта на втвърдяване.
Мисля, че опитен инспектор може да определи истинската причина за ниската твърдост, като организира и комбинира други методи за тестване, и след това да намери истинската причина за нейното разрешаване; като занаятчия, ако сте запознати с характеристиките на конвенционалните метални суровини, Охлаждащите характеристики на собственото оборудване и среда са достигнали определено ниво на разпознаване, което е от голяма помощ за формулирането на процеси на карборизиране и закаляване.
3. Неравномерна твърдост: равномерна температура на пещта (влияеща върху еднородността на карбуризиране), структура на оборудването, циркулация на атмосферата, натоварване на пещта (влияеща върху еднородността на карбуризиращия слой и в същото време влияеща върху равномерността на закаляването)
4. Твърдостта на сърцевината е неквалифицирана. Твърде висока: температурата на охлаждане е твърде висока, втвърдяването на материала е твърде добро, горната граница на състава на въглерод и сплав и средната скорост на охлаждане е твърде бърза. Твърдостта на сърцевината е ниска: точно обратното.
Пример за споделяне: 20 # стоманен 1.5 мм продукт, изисквания: инфилтрационен слой 0.2-0.4 mm сърцевина HV250, някои приятели от същата индустрия смятат, че изискванията са неразумни, (всеки трябва да знае, че най-високата твърдост на 20 # мартензит от стоманена плоча ще бъде HV450- 470) За да разрешим този проблем, първо трябва да разберем характеристиките на този материал: включително закалимост и закалимост.
След това комбинирайте гореспоменатите фактори, които влияят на охлаждащия ефект, и намерете начини за нагряване и охлаждане. В този случай материалът е фиксиран. Можем да намерим начин от температурата на охлаждане и скоростта на охлаждане. Този производител използва масло с превишена скорост. Ако намаляването на интензивността на охлаждане не отговаря на изискванията, можем също да намалим температурата на охлаждане. Метод.
Все още същото изречение, от 860-760 градуса, (когато температурата се понижи до определено ниво, от преохладения аустенит в сърцевината ще се утаи определено количество ферит и в този момент твърдостта ще намалее., Колкото повече температурата намалява, колкото повече се утаява ферит, толкова повече твърдостта намалява.
Ето напомняне: Необходимо е да се комбинират напълно съществуващите условия на оборудването и да се вдигне шум около специалния благоприятен индекс на плитка пропускливост.
3. Карбуризираният слой или ефективният карбуризиран слой е по-дълбок и по-плитък
Както бе споменато по-рано, дълбочината на инфилтрационния слой е цялостна функция на температурата, времето и концентрацията на въглерод. За да разрешим този проблем, трябва да започнем с температура на нагряване, скорост на нагряване, време на задържане, скорост на охлаждане и контрол на градиента на концентрацията на въглерод във въглеродния слой. Колкото по-висока е температурата, толкова по-дълго е времето и колкото по-висок е въглеродният потенциал, толкова по-дълбок е инфилтрационният слой и обратно.
Но всъщност е много повече от толкова просто. За да проектирате процес на карборизиране, трябва също да вземете предвид оборудването, капацитета на пещта, характеристиките на маслото, металографската структура, втвърдяването на материала, градиента на концентрацията на въглерод в карборизирания слой и скоростта на охлаждане. И много други фактори. Това може да се анализира с оглед на предишната ситуация с ниска твърдост и няма да бъде обяснено в дълбочина.
Четвърто, металографска организация
Прекомерен мартензит: суровината има груби зърна или не е нормализирана и температурата на карбуризиране е твърде висока. Решение: нормализиране или многократно нормализиране (препоръчително е нормализиращата температура да е с 20-30 градуса по-висока от температурата на карборизиране) Ако е възможно, помислете за карбуризиране и бавно охлаждане и след това за повторно загряване и охлаждане
Прекомерна параолимпийска: температурата на охлаждане е твърде висока, съдържанието на въглерод в аустенита е твърде високо (въглеродният потенциал е твърде висок). Решение: Пълната дифузия и условията позволяват да се намали температурата на охлаждане, закаляването и повторното нагряване и охлаждане при висока температура или криогенната обработка.
Прекомерен карбид: твърде високо съдържание на въглерод в аустенита (твърде висок въглероден потенциал), твърде бавен процес на охлаждане, утаяване на карбид
Решение: напълно дифузно, контролирайте скоростта на охлаждане, намалете възможно най-разликата в температурата между нагряване и закаляване и използвайте охлаждане с ниска температура или под температура възможно най-малко. Ако този процес трябва да се използва, натоварването на пещта трябва да се контролира. Нека си представим: същото оборудване се карбонизира при 920 ° C и се охлажда при 820 ° C. Капацитетът на пещта е 1000 кг и 600 кг, а скоростта на охлаждане е същата? Коя ще отнеме повече време? Коя карбидна степен е по-висока?
Петици. Неконско и вътрешно окисляване
Вътрешно окисление: Това е реакцията между легиращи елементи като хром, манган и молибден в стоманата и окислителната атмосфера в атмосферата (главно кислород, вода, въглероден диоксид), която изчерпва легиращите елементи в матрицата, което води до намаляване в втвърдяването на материала. Черната мрежова структура може да се види под микроскопа, нейната същност е структурата на троостита, получена от изчерпването на легиращите елементи в матрицата и намаляването на втвърдяването.
Решението е да се намерят начини да се увеличи скоростта на охлаждане на средата, да се увеличи интензивността на охлаждане и да се намали окислителната атмосфера в пещта (да се осигури чистотата на карбонизиращите суровини и спомагателни материали, да се сведе до минимум количеството балансиран въздух, да се контролира балансираният съдържание на въздушна влага и се уверете, че оборудването не изтича. Достатъчно отработени газове) Конвенционалното оборудване е трудно да се елиминира. Твърди се, че оборудването за вакуумиране под вакуум с ниско налягане може да бъде напълно елиминирано. В допълнение, мощното изстрелване може също да намали нивото на вътрешно окисление.
Прочетох мненията на някои експерти, а някои смятат, че прекомерният амоняк в процеса на карбонитриране също може да причини сериозни неконности. Аз лично имам различно мнение по този въпрос: може би това е причинено от прекомерно съдържание на вода в амоняк? Тъй като съм бил изложен на много процеси на карбонитриране, при проверка на продукта не е открита очевидна неконска тъкан. (Но не мисля, че тази гледна точка е погрешна) Някои чуждестранни машиностроения придават голямо значение на вътрешното окисляване, особено индустрията на зъбните колела. В национален мащаб дълбочината обикновено се изисква да бъде не повече от 0.02 mm според квалификацията.
Не-мартензитна: не-мартензитната структура се появява на повърхността на карборизирания слой поради проблеми с карборизацията или закаляването след закаляване, като ферит, бейнит и, разбира се, вътрешен тип окисление троостит. Механизмът на генериране е подобен на вътрешното окисление и разтворът е подобен.
Шест. Проблем с деформацията
Това е системен проблем и е най-проблемният проблем за нашия персонал, ангажиран с термична обработка. Гарантира се от няколко аспекта на охлаждащата среда на процеса на суровината. Горното съдържание е само личен опит. Ако има някакво несъответствие, можете да ме поправите, благодаря.
Моля, запазете източника и адреса на тази статия за повторно отпечатване:Събиране на често срещани дефекти и превантивни мерки при обезгаряването и закаляването
Мингхе Компания за леене на умира са посветени на производството и осигуряват качествени и висококачествени части за леене (обхватът на части за леене на метали включва главно Тънкостенно леене под налягане,Топъл камер Die Casting,Студено камерно леене), Кръгло обслужване (услуга за леене под налягане,Cnc обработка,Изработка на плесени, Повърхностна обработка). Всички персонализирани алуминиеви отливки, леене с магнезий или Zamak / цинк и други отливки са добре дошли да се свържете с нас.
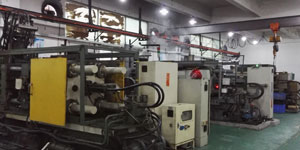
Под контрола на ISO9001 и TS 16949, всички процеси се извършват чрез стотици усъвършенствани машини за леене под налягане, 5-осни машини и други съоръжения, вариращи от бластери до Ultra Sonic перални машини. Minghe не само разполага с модерно оборудване, но и разполага с професионални екип от опитни инженери, оператори и инспектори, за да реализират дизайна на клиента.
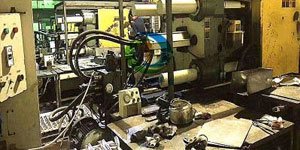
Договорен производител на отливки. Възможностите включват части за леене от алуминий със студена камера от 0.15 lbs. до 6 lbs., настройка за бърза смяна и обработка. Услугите с добавена стойност включват полиране, вибриране, отстраняване на обезкосмяването, струйно взривяване, боядисване, покритие, покритие, монтаж и обработка на инструменти. Материалите, с които се работи, включват сплави като 360, 380, 383 и 413.
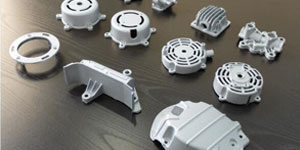
Помощ при проектиране на леене на цинк при съпътстващи инженерни услуги Персонализиран производител на прецизни отливки от цинкова матрица. Могат да се произвеждат миниатюрни отливки, отливки под високо налягане, отливки с многоплъзгащи се форми, конвенционални отливки за форми, единични матрици и независими отливки и отливки с кухина Отливките могат да се произвеждат с дължина и ширина до 24 инча в толеранс +/- 0.0005 инча.
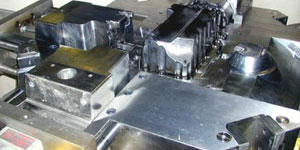
ISO 9001: 2015 сертифициран производител на магнезиево леене под налягане, Възможностите включват магнезиево леене под високо налягане до 200 тона гореща камера и 3000 тона студена камера, дизайн на инструментите, полиране, формоване, обработка, боядисване на прах и течности, пълен QA с CMM възможности , монтаж, опаковане и доставка.
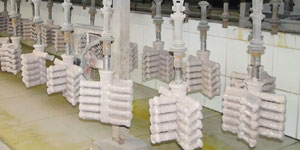
Сертифициран по ITAF16949 Включва допълнителна услуга за кастинг инвестиционно леене,пясъчно леене,Гравитационен кастинг, Изливане на пяна леене,Центробежно леене,Вакуумно леене,Постоянно леене на мухъл, .Възможностите включват EDI, инженерна помощ, солидно моделиране и вторична обработка.
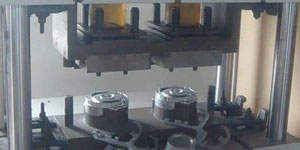
Кастинг индустрии Казуси за части за автомобили: Мотори, Самолети, Музикални инструменти, Водни плавателни съдове, Оптични устройства, Сензори, Модели, Електронни устройства, Кутии, Часовници, Машини, Двигатели, Мебели, Бижута, Конзоли, Телеком, Осветление, Медицински изделия, Фотографски устройства, Роботи, скулптури, озвучителна техника, спортна екипировка, инструментална екипировка, играчки и др.
Какво можем да ви помогнем да направите по-нататък?
∇ Отидете на началната страница за Китай за леене под налягане
→Части за леене-Разберете какво сме направили.
→ Съпоставени съвети за Услуги за леене под налягане
By Производител на леене под налягане Minghe | Категории: Полезни статии |Материал Tags: Алуминиево леене, Цинково леене, Магнезиево леене, Титаново леене, Леене от неръждаема стомана, Месинг леене,Бронзово леене,Кастинг на видео,История на компанията,Алуминиево леене под налягане | Коментарите са изключени