Влияещите фактори на термичната обработка на металните изковки
При производството на коване, освен да гарантира необходимата форма и размер на ковката, тя трябва да отговаря и на експлоатационните изисквания на детайла по време на употреба. Използвайки разумна технология за коване и параметри на процеса, организацията и структурата на суровините могат да бъдат подобрени чрез следните аспекти:
- Разчупете колонните кристали, подобрете макросегрегацията, променете отлитата структура в кована структура и при подходящи температурни и напрегнати условия заварете вътрешните кухини, за да увеличите плътността на материала;
- Слитката се кова, за да се образува влакнеста структура, а по -нататъшното валцуване, екструдиране и коване на матрици се използват за получаване на разумно разпределение на посоката на влакното за коване;
- Контролирайте размера и равномерността на кристалните зърна;
- Подобряване на разпределението на втората фаза (като сплави от карбиди в твърд ледебурит);
- Структурата се подсилва чрез деформация или деформационно-фазова трансформация.
Поради подобряването на гореспоменатата структура, пластичността, ударната издръжливост, якостта на умора и издръжливостта на изковките също са подобрени, а след това чрез крайната термична обработка на частите, добра комбинация от твърдост, здравина и пластичност, изисквана от частите могат да бъдат получени. производителност.
Ако използваният процес на коване е необоснован, той може да доведе до дефекти на коване, включително повърхностни дефекти, вътрешни дефекти или неквалифицирани характеристики, което ще повлияе на качеството на обработка на последващите процеси, а някои сериозно ще повлияят на работата на изковките и ще намалят качеството на готовите продукти . Срокът на експлоатация на батерията може дори да застраши безопасността.
Влиянието на ковашката структура върху структурата и свойствата след крайната термична обработка се проявява главно в следните аспекти:
- Непоправими структурни дефекти: аустенитни и феритни топлоустойчиви неръждаеми стомани, високотемпературни сплави, алуминиеви сплави, магнезиеви сплави и др., Материали, които нямат изомерна трансформация при нагряване и охлаждане, както и някои медни сплави и за титанови сплави, структурните дефекти, генерирани по време на процеса на коване, не могат да бъдат подобрени чрез термична обработка.
- Организационни дефекти, които могат да бъдат подобрени: едрозърнеста и Widmanstatten структура като цяло прегряти конструкционни стоманени изковки, леки мрежести карбиди, причинени от неправилно охлаждане на хиперевтектоидни стомани и носещи стомани по време на термична обработка след коване, Удовлетворителна структура и експлоатационни характеристики могат да бъдат постигнати след окончателното термична обработка на коване (3) Организационни дефекти, които са трудни за отстраняване чрез нормална термична обработка: като едрозърнесто с ниско увеличение, неръждаема стомана 9Cr18, двойни карбиди от Н13 и др., изискват нормализиране при висока температура, многократно нормализиране, нискотемпературно разлагане, високотемпературно дифузионно отгряване и други мерки, които трябва да бъдат подобрени.
- Организационни дефекти, които не могат да бъдат елиминирани чрез общия процес на термична обработка: сериозни счупвания на камъни и счупвания на хребети, прегаряне, феритни ленти от неръждаема стомана, карбидни мрежи и ленти от легирана легирана инструментална стомана и др. Производителността на изковките след термична обработка намалява или дори се проваля.
- Дефекти на микроструктурата, които допълнително ще се развият по време на крайната термична обработка: Например грубозърнестата структура в изкованите конструкции от легирана стомана, ако термичната обработка след коване не се подобри, често причинява мартензит след въглерод, азотиране и закаляване Иглата е дебела и изпълнението е неквалифицирано; дебели лентови карбиди от високоскоростна стомана често причиняват напукване по време на закаляването.
- Ако отоплението е неправилно, например, температурата на нагряване е твърде висока и времето за нагряване е твърде дълго, това ще доведе до дефекти като декарбуризация, прегряване и прегряване.
- По време на процеса на охлаждане след коване, ако процесът е неправилен, това може да причини охлаждащи пукнатини, бели петна и т.н., които могат да се напукат по време на термичната обработка.
Какви са ефектите от рязането върху качеството на термично обработените детайли?
- В състояние на закаляване и закаляване, отгряване и нормализиране на детайла, твърдостта е по-ниска от 45 HRC, а качеството на детайла, включително повърхностното покритие, остатъчното напрежение, надбавката за обработка и отстраняването на слоя, обеднен от въглерод на повърхността, не е повлияни от процеса на рязане. Очевидно това няма да доведе до промяна в потенциалните характеристики на детайла.
- Обработката на детайли от закалена стомана или детайли се нарича още твърда обработка. Твърдостта на детайлите достига 50 ~ 65 HRC. Материалите включват основно обикновена закалена стомана, закалена матрица, лагерна стомана, валцувана стомана и високоскоростна стомана и др. Въздействието на рязането е по-очевидно. Фактори като генериране и провеждане на топлина на рязане, високоскоростно триене и износване по време на процеса на рязане ще причинят определена степен на повреда на обработваната повърхност. Целостта на обработваната повърхност по време на твърдо рязане включва главно повърхностната текстура, твърдостта, грапавостта на повърхността, точността на размерите, разпределението на остатъчното напрежение и образуването на бял слой.
Твърдостта на обработваната повърхност се увеличава с увеличаването на скоростта на рязане и намалява с увеличаването на скоростта на подаване и количеството на рязане. И колкото по -висока е твърдостта на обработената повърхност, толкова по -голяма е дълбочината на втвърдения слой. Резултатите показват, че равномерното остатъчно напрежение на натиск върху повърхността на детайла след твърдо рязане, докато максималното напрежение на натиск на детайла след смилане е концентрирано главно върху повърхността на детайла.
Колкото по -голям е радиусът на тъп ъгъл на инструмента, толкова по -голяма е стойността на остатъчното напрежение на натиск; колкото по -висока е твърдостта на детайла, толкова по -голяма е стойността на остатъчното напрежение на натиск. Твърдостта на детайла оказва голямо влияние върху целостта на повърхността на детайла. Колкото по -голяма е твърдостта на детайла, толкова по -благоприятно е за образуването на остатъчно напрежение при натиск.
Друг важен фактор, който влияе върху качеството на повърхността при твърдо рязане, е образуването на бели слоеве. Белият слой е структура, образувана от процеса на твърдо рязане. Той има уникални характеристики на износване: от една страна, има висока твърдост и добра корозионна устойчивост; от друга страна, той показва висока крехкост, която е лесна за причиняване на ранна повреда при отлепване. Може дори да се напука, след като бъде поставен за етап след обработката. При рязане на закалена лагерна стомана AISIE52100 с керамични и PCBN инструменти на CNC струг с висока твърдост е установено, че повърхностните и подповърхностните слоеве на детайла са се променили в тяхната микроструктура. Микроструктурата се състои от бял нетемпериран слой и черен прекалено закален слой.
Понастоящем мнението, че белият слой се разглежда като мартензитна структура, е единодушно признато и основният спор е в фината структура на белия слой. Едно мнение е, че белият слой е резултат от смяна на фазата и се състои от финозърнест мартензит, образуван от бързо нагряване и внезапно охлаждане на материала по време на процеса на рязане. Друг възглед е, че образуването на белия слой е само термин на деформационен механизъм, който е просто нетрадиционен мартензит, получен чрез пластична деформация.
Моля, запазете източника и адреса на тази статия за повторно отпечатване:Влияещите фактори на термичната обработка на металните изковки
Мингхе Компания за леене на умира са посветени на производството и осигуряват качествени и висококачествени части за леене (обхватът на части за леене на метали включва главно Тънкостенно леене под налягане,Топъл камер Die Casting,Студено камерно леене), Кръгло обслужване (услуга за леене под налягане,Cnc обработка,Изработка на плесени, Повърхностна обработка). Всички персонализирани алуминиеви отливки, леене с магнезий или Zamak / цинк и други отливки са добре дошли да се свържете с нас.
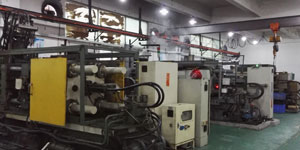
Под контрола на ISO9001 и TS 16949, всички процеси се извършват чрез стотици усъвършенствани машини за леене под налягане, 5-осни машини и други съоръжения, вариращи от бластери до Ultra Sonic перални машини. Minghe не само разполага с модерно оборудване, но и разполага с професионални екип от опитни инженери, оператори и инспектори, за да реализират дизайна на клиента.
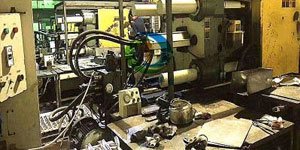
Договорен производител на отливки. Възможностите включват части за леене от алуминий със студена камера от 0.15 lbs. до 6 lbs., настройка за бърза смяна и обработка. Услугите с добавена стойност включват полиране, вибриране, отстраняване на обезкосмяването, струйно взривяване, боядисване, покритие, покритие, монтаж и обработка на инструменти. Материалите, с които се работи, включват сплави като 360, 380, 383 и 413.
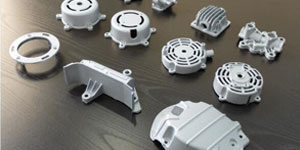
Помощ при проектиране на леене на цинк при съпътстващи инженерни услуги Персонализиран производител на прецизни отливки от цинкова матрица. Могат да се произвеждат миниатюрни отливки, отливки под високо налягане, отливки с многоплъзгащи се форми, конвенционални отливки за форми, единични матрици и независими отливки и отливки с кухина Отливките могат да се произвеждат с дължина и ширина до 24 инча в толеранс +/- 0.0005 инча.
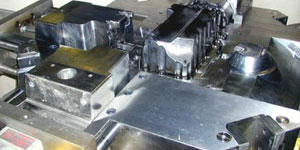
ISO 9001: 2015 сертифициран производител на магнезиево леене под налягане, Възможностите включват магнезиево леене под високо налягане до 200 тона гореща камера и 3000 тона студена камера, дизайн на инструментите, полиране, формоване, обработка, боядисване на прах и течности, пълен QA с CMM възможности , монтаж, опаковане и доставка.
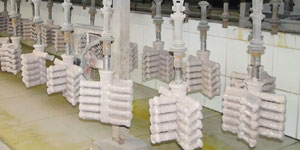
Сертифициран по ITAF16949 Включва допълнителна услуга за кастинг инвестиционно леене,пясъчно леене,Гравитационен кастинг, Изливане на пяна леене,Центробежно леене,Вакуумно леене,Постоянно леене на мухъл, .Възможностите включват EDI, инженерна помощ, солидно моделиране и вторична обработка.
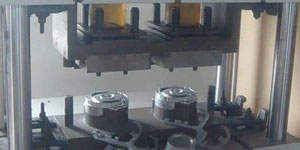
Кастинг индустрии Казуси за части за автомобили: Мотори, Самолети, Музикални инструменти, Водни плавателни съдове, Оптични устройства, Сензори, Модели, Електронни устройства, Кутии, Часовници, Машини, Двигатели, Мебели, Бижута, Конзоли, Телеком, Осветление, Медицински изделия, Фотографски устройства, Роботи, скулптури, озвучителна техника, спортна екипировка, инструментална екипировка, играчки и др.
Какво можем да ви помогнем да направите по-нататък?
∇ Отидете на началната страница за Китай за леене под налягане
→Части за леене-Разберете какво сме направили.
→ Съпоставени съвети за Услуги за леене под налягане
By Производител на леене под налягане Minghe | Категории: Полезни статии |Материал Tags: Алуминиево леене, Цинково леене, Магнезиево леене, Титаново леене, Леене от неръждаема стомана, Месинг леене,Бронзово леене,Кастинг на видео,История на компанията,Алуминиево леене под налягане | Коментарите са изключени