Как да осигурим стабилността на системата със зелен пясък?
I. Въведение
Поради промени в производствените условия и околната среда неизбежно ще се променят други параметри на отливката. Ако процесът на формоване на пясък не може да се регулира навреме, пясъчната система ще бъде нестабилна, което в крайна сметка ще доведе до по -трудно почистване на отливката или дори скрап;
По този начин е необходимо да се регулира първоначалният процес на формоване на пясък, за да се стабилизира пясъчната система; материалният състав на формовъчния пясък се състои главно от стар пясък, суров пясък, бентонит и добавки. Тъй като повече от 95% от формовъчния пясък е стар пясък, а старият пясък се влияе от фактори като различното съотношение пясък към желязо при отливката и различното количество смесване на пясъка от сърцевината, което води до много големи колебания в състав на материала. Следователно, за да се контролира състава на формовъчен пясък, е необходимо да се провери ефективното съдържание на бентонит, ефективно съдържание на добавки и кал в формоващия пясък, за да се определи добавеното количество бентонит, добавки и суров пясък по време на смесването на пясък.
Тази статия ще представи накратко как леярната на компанията на автора се корени в реалния производствен процес.
Според промяната на параметрите процесът на формоване на пясък се регулира, за да се гарантира стабилността на пясъчната система.
2. Определяне на ключови параметри за формоване на пясък:
1. Ефективно съдържание на бентонит: Ефективното съдържание на бентонит (активно) се определя въз основа на характеристиките на минерала монтморилонит, съдържащ се в бентонита, който може да абсорбира метиленово синьо и други багрила; той се отнася до титруване на 5.00 g формовъчен пясък с 0.20% концентрат реагент чист разтвор на метиленово синьо [mL]; преобразуван съгласно стандартната формула на кривата на бентонит (%)
2. Ефективна дозировка на добавките: Сравнява се с отделянето на газ при добавките за формовъчен пясък и се изчислява по формулата; т.е. отделянето на газ от 1.00 g формовъчен пясък при 900 ° C [mL] минус отделянето на газ от активирания бентонит в формовъчния пясък (средното количество, измерено преди изчислението) След това сравнете с 1g обем газ добавка (%).
3. Кално съдържание: Съгласно националния стандарт GB/T9442-1998, фините прахови частици с диаметър по-малък от 20 μm се определят като кал. Утайката обикновено се отстранява чрез промивен метод [2].
4. Размер на частиците от формован пясък: изразен в AFS финост, тоест средният размер на пясъчните частици се отразява според въображаемата марка на ситото [3];
5. Метод за изчисляване на фината AFS: Процедурите за измерване на фината AFS и методите за изчисление, посочени от Американския институт по леярство, са както следва:
①. Първо се претеглят около 50 g от пясъчната проба, която се измерва, отмива се калта, подсушава се и след това се пресява
②. Претеглете и запишете качеството на пясъчните частици, останали на всяко сито;
③. Изчислете процента от количеството пясъчни частици, останали на всяко сито, към общото количество пясъчни проби;
④. Умножете процента от количеството пясъчни частици, останали на всяко сито, с „множителя за финост на AFS“, съответстващ на всяко сито;
⑤. Добавете горните продукти за всеки номер на сито, за да намерите сумата:
⑥. Разделете получената сума в т. 5 на сумата от процентите на задържания пясък на всяко сито в т. 3, за да се получи фината AFS
3. План за корекция:
Използваното от фабриката оборудване за смесване на пясък е пясъчна мелница DISA и оборудване за формоване KW линия за формоване на статично налягане; използвайки статистически данни за половин година, са формулирани следните планове за неговата система за формоване с пясък:
1. Статистика:
① Определете количеството на формовъчния пясък, добавен към всяка кутия, според стойността на настройка на формоването, и изчислете съотношението пясък към желязо на всяка кутия от отливки според теглото на всяка кутия от отливки и теглото на изливането система и количеството основен пясък, използван при леенето;
Статистика за количеството изхвърлен отпадъчен пясък и използването на основен пясък и спомагателни материали
③ Статистика за отстраняване на прах от системата за формоване на пясък
2. Регулиране на пясъка:
① Според производствената ситуация, когато леенето се произвежда непрекъснато в продължение на два или повече дни, добавеното количество формовъчни пясъчни аксесоари (бентонит, добавки) се фиксира и промените в ефективното количество формовъчен пясък се отчитат, и след това постепенно се проверява по време на непрекъснатото производство на други отливки Връзката между съотношението пясък към желязо и добавеното количество;
② Регулиране на размера на частиците от формовъчен пясък: коригирайте според средната стойност на сито 50/100 (силициев пясък на сито 50/100, средната стойност на средната финост е 50 [4]), когато AFS на формования пясък е по-малко или равно на 50, чрез добавяне на фин пясък 70/140 или по-фин нов пясък 140/70 се регулира, добавя се 30 кг-60 кг на мелница и се анализира промяната в размера на частиците.
Регулиране на съдържанието на кал в формовъчния пясък: анализирайте промяната на съдържанието на кал в системата за формоване на пясък чрез статистиката за ежедневното отстраняване на прах;
Четвърто, специфичният процес на настройка:
1. Статистика на съотношението на леярския пясък към желязото:
(Забележка: Тъй като корпусът на цилиндъра X2B1 е излят с интегрирана пясъчна сърцевина, той няма да изгори формования пясък, така че теглото на външния формовъчен пясък на отливката се изчислява като "0")
2. Регулирайте ефективното количество според съотношението пясък към желязо на отливката. Съотношението пясък към желязо на цилиндровия блок 56D е 6.57. Сред горните отливки, съотношението пясък към желязо е най-високото сред отливките на блока на цилиндрите. Следователно 56D цилиндровият блок първо се тества:
Когато 56D се произвежда в продължение на три последователни дни, количеството на добавката е 22 kg/mill, а количеството добавка на глина е 33kg/mill; ефективното количество добавки нарасна от 4.55% на 5.03%; ефективното количество глина се е повишило от 6.56% на 7%; увеличение с около 0.5 %; Това означава, че когато се произвежда цилиндър 56D, добавеното количество трябва да се регулира така, че да е по -високо от балансовата стойност на пясъчната система;
Чрез горния анализ на данните количеството добавени помощни материали се коригира, както следва:
1) Когато цилиндърът се възпроизвежда, количеството на добавката се коригира до 19 кг/мел, а когато количеството добавка на глина е 26 кг/мел, статистическите данни за три последователни дни показват, че ефективното количество добавки се е променило от 4.36% на 4.29% ; ефективното количество глина се е променило от 4.36% на 4.29%. 7.22% става 7.11%; ефективното количество се колебае с 0.1%; следователно планът за регулиране на процеса е разумен и може да осигури баланса на системата за формоване на пясък;
2) По същия начин връзката между количеството помощни материали, добавени към други отливки, и ефективното количество се изчислява чрез експериментален анализ на данни и теория; когато възпроизвеждате различни отливки, коригирайте подходящото количество добавени помощни материали.
3. Използвайте нов пясък 70/140 окото и 140/70 нов пясък, за да регулирате размера на пясъка (съдържанието на кал в прототипния пясък е 11.42%):
① От 16 януари до 21 януари, общо 4257 пъти смилане на пясък за пет дни, около 4257*3/900 = 14 пъти; размерът на частиците на всеки цикъл се променя около 0.26 (за смилане); следователно формовъчният пясък на 16 януари AFS стойността е 49.15; от 16 януари, пет дни непрекъснато добавяне на 70/140 нов пясък за регулиране на размера на частиците, 60 кг на мелница, стойността на AFS на формовъчния пясък на 21 януари е 52.84;
② От 25 януари до 27 януари общо 2165 пъти смилане на пясък за три дни, приблизително 2165*3/900 = 7 цикъла; размерът на зърната на всеки цикъл се променя приблизително 0.22 (за смилане); следователно, 24 януари пясък AFS = 52.44, когато размерът на частиците на формовъчния пясък достигне 52-53, непрекъснатото добавяне на 70/140 нов пясък има малък ефект върху пясъчната система AFS; от 26 януари се добавя 140/70 нов пясък за три последователни дни, за да се коригира, и се добавя 60 кг за всяко смилане, 1 На 28 -и AFS на пясъка е 54.
(Забележка: ①Стандарта на предприятието FAW предвижда, че процентът на пресяване на 70/140 кварцов пясък 70,100,140 ≥80%, от които 70,100 пресяване ≥60%; 140/70 кварцов пясък 70,100,140 процент на пресяване ≥80%, от които 100,140 процент на пресяване ≥60 % ② Всеки обем на смилане е 3 тона, а обемът на системния пясък се оценява на 900 тона)
4. Сравнение на съдържанието на кал и отстраняване на прах за три последователни месеца:
Поради студения климат на север от февруари до март прахът в тръбопровода за студено отстраняване на прах ще се кондензира и втвърди след отстраняването на горещия прах. Ако тръбопроводът не бъде почистен навреме, често ще възникнат запушвания, а дневният разряд ще варира от 4 до 8 тона. Съдържанието на кал в пясъчната система варира значително. През този период единственият начин да увеличите капацитета за отстраняване на прах и да намалите съдържанието на кал е чрез увеличаване на обема на въздуха на оборудването за отстраняване на прах и драгиране на тръбите;
След навлизането през април температурата постепенно се повишава, феноменът на кондензация на прах и втвърдяване вече не се появява, количеството на отстраняване на прах постепенно се стабилизира, достигайки среден разход от 7-8 тона на ден, а диапазонът на колебания на съдържанието на кал се намалява;
Съдържанието на кал в системата за формоване на пясък може също да бъде намалено чрез добавяне на нов пясък или намаляване на добавянето на помощни материали. Недостатъците на тези два метода ще бъдат обяснени в заключението на теста.
5. Заключение от теста
1. Регулирайте ефективното количество пясъчни принадлежности
Кристалите на бентонита се повреждат до известна степен при нагряване и силата на мокро свързване очевидно ще намалее след добавяне на вода и смесване. След нагряване при по -висока температура и по -дълго време, кристалната структура на бентонита се разрушава напълно и той става „мъртва глина“ без кохезионна сила. Увеличената дебелина на леене, ниското съотношение пясък към желязо, високата температура на изливане и дългото време на охлаждане увеличават загубите при изгаряне на бентонита.
Най -директният начин да се прецени дали ефективният въглен прах в формования пясък е достатъчен е да се наблюдава гладкостта на повърхността на отливката и дали има залепване на пясък. Част от въглищата в стария пясък се изгарят поради топлината на излятия разтопен метал и трябва да се попълни. От друга страна, трябва да се добавят ново добавени материали като пресен пясък, пясък със смесена сърцевина и бентонит, за да се постигне нивото на ефективни прахообразни въглища. Общото количество прахообразни въглища, добавено по време на смесването на пясък, е сумата от загубите при изгаряне и допълнителното допълнително количество. (Ефективният въглищен прах е еквивалентен на ефективната добавка в текста)
2. Регулиране на размера на пясъка:
Размерът на частиците на формовъчния пясък под високо налягане обикновено е 50/140, докато размерът на частиците от смолисти пясъчни ядра е предимно 50/100 или по-груб. Прекомерното смесване на основния пясък ще повлияе на огрубяването на целия стар мокър пясък, което ще увеличи пропускливостта на пясъка и грапавата повърхност на отливката.
За да се предотврати натрупването на размера на частиците на формования пясък, частиците от системата за отстраняване на прах могат да се рециклират в стария пясък. Или добавете фин нов пясък, за да регулирате; както е споменато в леярната, когато AFS на формовъчния пясък достигне около 48, регулирайте, като непрекъснато добавяте 70/140 или 140/70 нов пясък; обаче, тъй като отливките се разбиват в сърцевината на пясъчната система Количеството пясък вече е голямо. Ако размерът на частиците на формовъчния пясък не е уплътнен в непоносима степен, не се препоръчва непрекъснато да се добавя толкова голямо количество нов пясък, в противен случай това ще повлияе на други показатели за ефективност на системата за формоване на пясък (съдържание на кал, ефективно количество и якост поради прекомерното количество нов пясък). ) имат влияние върху;
3. Регулиране на съдържанието на кал
Увеличаването на съдържанието на кал ще доведе до намаляване на пропускливостта на формовъчния пясък и явлението „експлозия на газ“ ще настъпи по време на процеса на изливане, а отливката ще бъде бракувана поради експлозията и лепкавия пясък. Съдържанието на кал в системата за формоване на пясък не трябва да бъде твърде високо; съдържанието на кал в пясъчната система може да бъде намалено чрез намаляване на количеството спомагателни материали, но намаляването на ефективното съдържание на бентонит ще доведе до намаляване на здравината на формования пясък и ще се намали способността за повдигане и устойчивост на пясък; ефективната доза на Намаляване ще доведе до намаляване на способността на пясъка против залепване на формоващия пясък.
Ако увеличите количеството на добавения нов пясък, за да коригирате съдържанието на кал, първо изчислете колко кал произвеждат различните новодобавени материали в леения пясък, а след това можете да изчислите колко суров пясък трябва да се добави, за да се получи съдържанието на кал в формовъчният пясък отговаря на процедурните правила.
Както бе споменато в статията, съдържанието на кал може да бъде намалено с 0.1% на всеки 30 кг нов пясък, добавен в леярната; прекомерното добавяне на нов пясък обаче не само ще доведе до загуба на разходи, но също така ще намали дела на използвания пясък в системата за формоване на пясък, което ще намали работата на формовъчния пясък. , Формовъчният пясък се разминава, което влияе върху способността на формовъчния пясък да се формира, а феноменът на измиване на пясък възниква по време на процеса на леене;
Следователно авторът смята, че е най -добрият избор, ако съдържанието на кал в пясъчната система може да се контролира чрез регулиране на оборудването за отстраняване на прах.
Като цяло стабилизираната пясъчна система трябва да може да произвежда висококачествени отливки. Чрез тази концепция ние трябва непрекъснато да коригираме процеса на формоване на пясък според променящите се производствени условия, за да отговорим на производствените нужди.
Моля, запазете източника и адреса на тази статия за повторно отпечатване: Как да осигурим стабилността на системата със зелен пясък?
Мингхе Компания за леене на умира са посветени на производството и осигуряват качествени и висококачествени части за леене (обхватът на части за леене на метали включва главно Тънкостенно леене под налягане,Топъл камер Die Casting,Студено камерно леене), Кръгло обслужване (услуга за леене под налягане,Cnc обработка,Изработка на плесени, Повърхностна обработка). Всички персонализирани алуминиеви отливки, леене с магнезий или Zamak / цинк и други отливки са добре дошли да се свържете с нас.
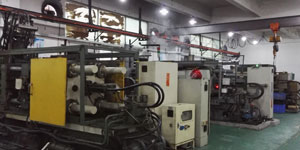
Под контрола на ISO9001 и TS 16949, всички процеси се извършват чрез стотици усъвършенствани машини за леене под налягане, 5-осни машини и други съоръжения, вариращи от бластери до Ultra Sonic перални машини. Minghe не само разполага с модерно оборудване, но и разполага с професионални екип от опитни инженери, оператори и инспектори, за да реализират дизайна на клиента.
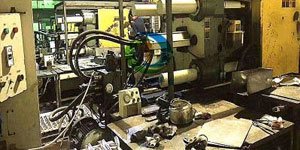
Договорен производител на отливки. Възможностите включват части за леене от алуминий със студена камера от 0.15 lbs. до 6 lbs., настройка за бърза смяна и обработка. Услугите с добавена стойност включват полиране, вибриране, отстраняване на обезкосмяването, струйно взривяване, боядисване, покритие, покритие, монтаж и обработка на инструменти. Материалите, с които се работи, включват сплави като 360, 380, 383 и 413.
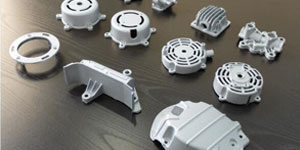
Помощ при проектиране на леене на цинк при съпътстващи инженерни услуги Персонализиран производител на прецизни отливки от цинкова матрица. Могат да се произвеждат миниатюрни отливки, отливки под високо налягане, отливки с многоплъзгащи се форми, конвенционални отливки за форми, единични матрици и независими отливки и отливки с кухина Отливките могат да се произвеждат с дължина и ширина до 24 инча в толеранс +/- 0.0005 инча.
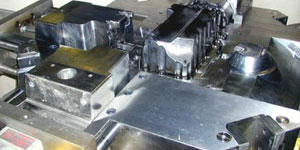
ISO 9001: 2015 сертифициран производител на магнезиево леене под налягане, Възможностите включват магнезиево леене под високо налягане до 200 тона гореща камера и 3000 тона студена камера, дизайн на инструментите, полиране, формоване, обработка, боядисване на прах и течности, пълен QA с CMM възможности , монтаж, опаковане и доставка.
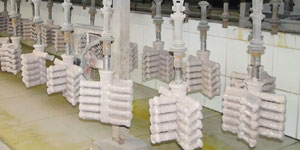
Сертифициран по ITAF16949 Включва допълнителна услуга за кастинг инвестиционно леене,пясъчно леене,Гравитационен кастинг, Изливане на пяна леене,Центробежно леене,Вакуумно леене,Постоянно леене на мухъл, .Възможностите включват EDI, инженерна помощ, солидно моделиране и вторична обработка.
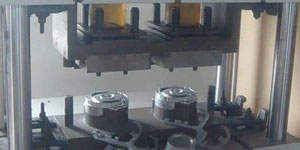
Кастинг индустрии Казуси за части за автомобили: Мотори, Самолети, Музикални инструменти, Водни плавателни съдове, Оптични устройства, Сензори, Модели, Електронни устройства, Кутии, Часовници, Машини, Двигатели, Мебели, Бижута, Конзоли, Телеком, Осветление, Медицински изделия, Фотографски устройства, Роботи, скулптури, озвучителна техника, спортна екипировка, инструментална екипировка, играчки и др.
Какво можем да ви помогнем да направите по-нататък?
∇ Отидете на началната страница за Китай за леене под налягане
→Части за леене-Разберете какво сме направили.
→ Съпоставени съвети за Услуги за леене под налягане
By Производител на леене под налягане Minghe | Категории: Полезни статии |Материал Tags: Алуминиево леене, Цинково леене, Магнезиево леене, Титаново леене, Леене от неръждаема стомана, Месинг леене,Бронзово леене,Кастинг на видео,История на компанията,Алуминиево леене под налягане | Коментарите са изключени